To get the most from miniature motion technology, a key design specification is whether to configure the motor with an inner or an outer rotor. This consideration is highly relevant to torque requirements, and it also has an impact on footprint and thermal design. Due to the motor’s vital role in applications ranging from medical devices to drones, it’s beneficial to involve a motion designer that can take the objectives of an original equipment manufacturer (OEM) and customise the solution accordingly.
Like every electric motor, miniature brushed DC motors, as well as their brushless DC (BLDC) counterparts, are based around a rotor and a stator. The stator’s role is to create a magnetic field that interacts with the rotor, which is embedded with magnets. It’s this interaction that causes the rotor to spin, driving the motor’s shaft.
Most commonly, the rotor is on the interior of the motor and the stator is part of the exterior. Conversely, in an outer rotor design, the rotor surrounds the stator. In this configuration, the motor’s stationary component is on the inside, while the rotating component spins around it.
For OEM design engineers, this distinction, and the choice between the two designs, is relevant because of the impact the selection has, relative to the output requirements of the given application. The position of the rotor can impact crucial aspects such as torque, inertia and heat dissipation – attributes that are likely to be critical to the overall performance characteristics of a machine’s design.
Torque generation
An outer rotor topology provides increased physical space to enable a higher number of magnetic poles compared to inner rotor technology. Created by the arrangement of magnets or electromagnetic windings, the poles are key, as it’s their interaction with the current supplied to the motor that ultimately generates motion. The higher the pole count, the greater the torque that can be generated, because of the frequency of magnetic interactions per rotation.
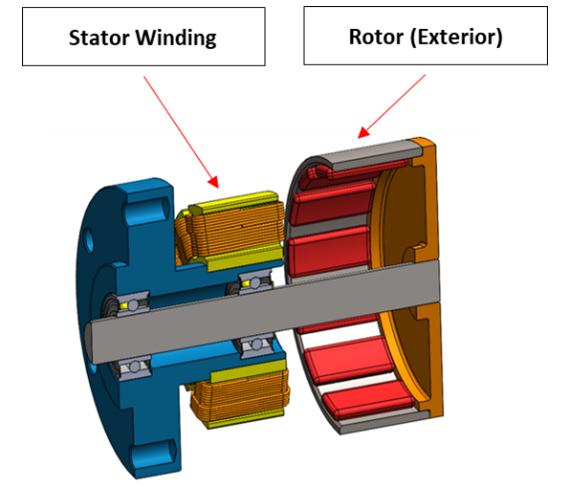
Outer Rotor Motor Construction.
With a rotor around the stator, its larger diameter also contributes to increased leverage. This effect enhances the motor’s ability to exert greater torque, thanks to the larger radius at which the magnetic force is applied.
Moreover, outer rotor motors can also achieve higher torque density, and more power, than comparative inner rotor motors. For a given power, outer rotor motors have a lower length-to-diameter ratio, which makes them compact and flat in design.
Responsiveness and efficiency
Conversely, inner rotor motors have lower inertia compared to outer rotor motors, which enables higher acceleration, a faster response, and a lower mechanical time constant. This is possible thanks to the rotor’s smaller mass, as well as its closer proximity to the axis of rotation. When an outer rotor motor design is specified, to combat the inertia, material selection and weight reduction are critical. This design will also need greater attention regarding rotor balancing to reduce noise and vibration, as well as to optimise bearing life.
Inner rotor motors are also more thermally efficient than their outer rotor counterparts, with less hindrance from the limiting factor of heat accumulation. While the rotor is on the inside, their stator, and hence their windings, are positioned on the outside, enabling easier heat dissipation. In contrast, outer rotor motors, with their internal windings, typically require innovative cooling solutions to maximise operational life.
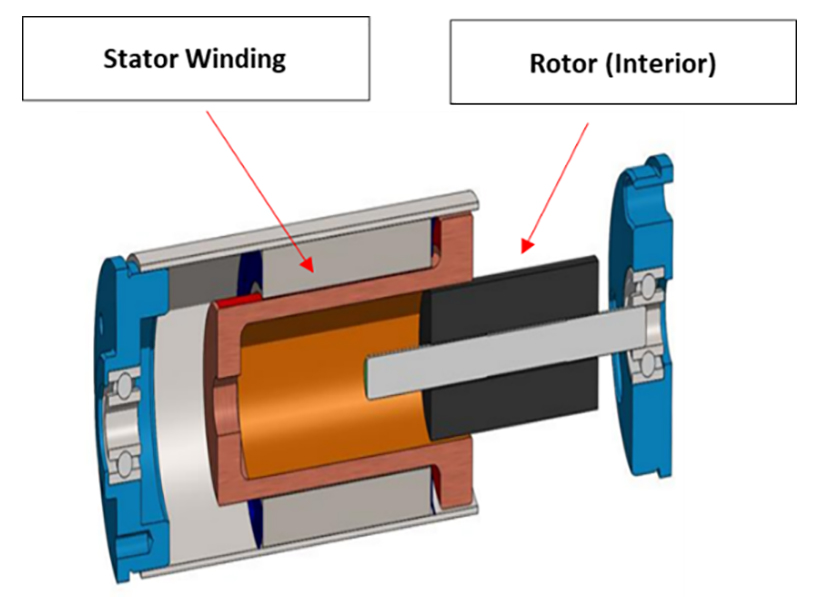
A traditional Inner Rotor Motor.
With lower inertia and improved thermal management, this also makes inner rotor motors more efficient. Contributing to this, inner rotor designs also usually have a smaller air gap between the stator and rotor. This results in more effective magnetic field interactions, which improves electromagnetic efficiency.
Real-world applications
With inner rotor designs, as the rotating component is enclosed within the stator, this effectively creates a barrier that reduces the exposure of the motor’s internal components to external contaminants. The enclosed design minimises gaps, offering greater sealing potential against particles and moisture. As a result, inner rotor motors are often preferred for applications with the most challenging environmental conditions.
That said, outer rotor motors can still be sufficiently protected for use in rugged locations and more challenging environments. Consequently, the advantage of their high torque characteristics within a compact footprint, for applications that need relatively low speed, can be leveraged for e-bikes, drones, and surgical robots. Alternatively, inner rotor motors excel in high-speed, lower-torque applications, such as medical devices and industrial tools.
Although an off-the-shelf motor design might fulfil a design team’s needs, more commonly, some level of customisation is required to optimise characteristics for the given application. Portescap’s engineers regularly collaborate with OEMs to provide a motion solution specific to a task. As well as having a strong design platform to work from, involving the motion solution designer early in the project means that a fast time to market can still be achieved. At the same time, this approach can optimise motion performance, reliability, and service life.