If you want to move something, you have to be able to control the movement. When positioning in the nanometer range everything matters and requires high performance motion control. Six years ago, Aerotech therefore set itself the goal of revolutionizing the market for precision motion and machine control systems. The Automation1 motion control platform, which was developed in-house and has been available since 2019, now offers far more capability than many users expect from a motion control system.
9 functions you wouldn’t expect from a motion controller
1. Control positioning systems and connected components such as servo and
stepper motors, galvo scan heads, piezoelectric actuators and various other
devices on one platform
2. Setup Assistant for the homing configuration of Gantrys
3. Camera module to display feed from a vision system that can be used to
monitor the automation and production process in addition to motion control
4. Intuitive configuration wizard for complete machine setup and rapid
implementation of projects
5. EasyTune servo tuning optimises the servo loop like a control engineer would
with access to third-party devices
6. HyperWire bus for drive connection, currently the most powerful
communication bus in the motion control industry
7. MachineApps HMI development tool for customizing user interfaces for drive
systems and allowing support for custom module development for ultimate
flexibility.
8. EtherCAT compatibility for simple and seamless integration of PLC-based
systems
9. Python API and Driver for LabVIEW that enable direct access to the motion
control platform.
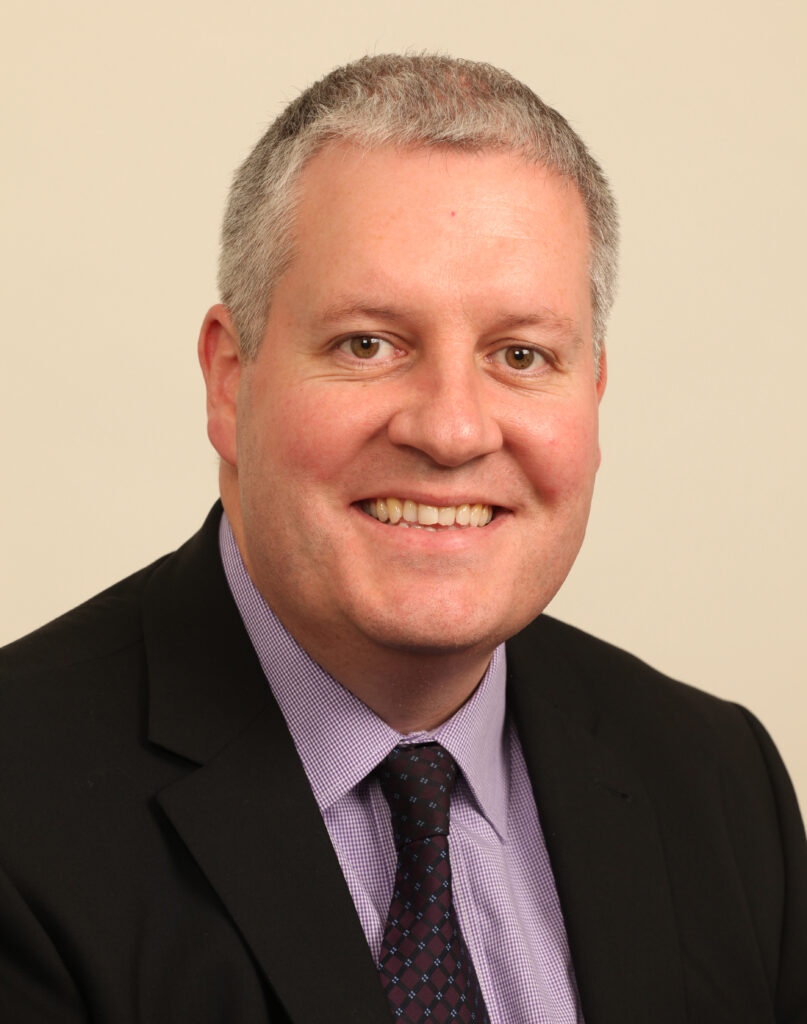
Simon Smith, European Director of Aerotech in Basingstoke: “The high-precision
control of motion components has been our expertise for decades. Whether in industry or in
research facilities, our solutions and systems are used wherever something needs to be
positioned with repeat accuracy in the micro and nanometer range.”
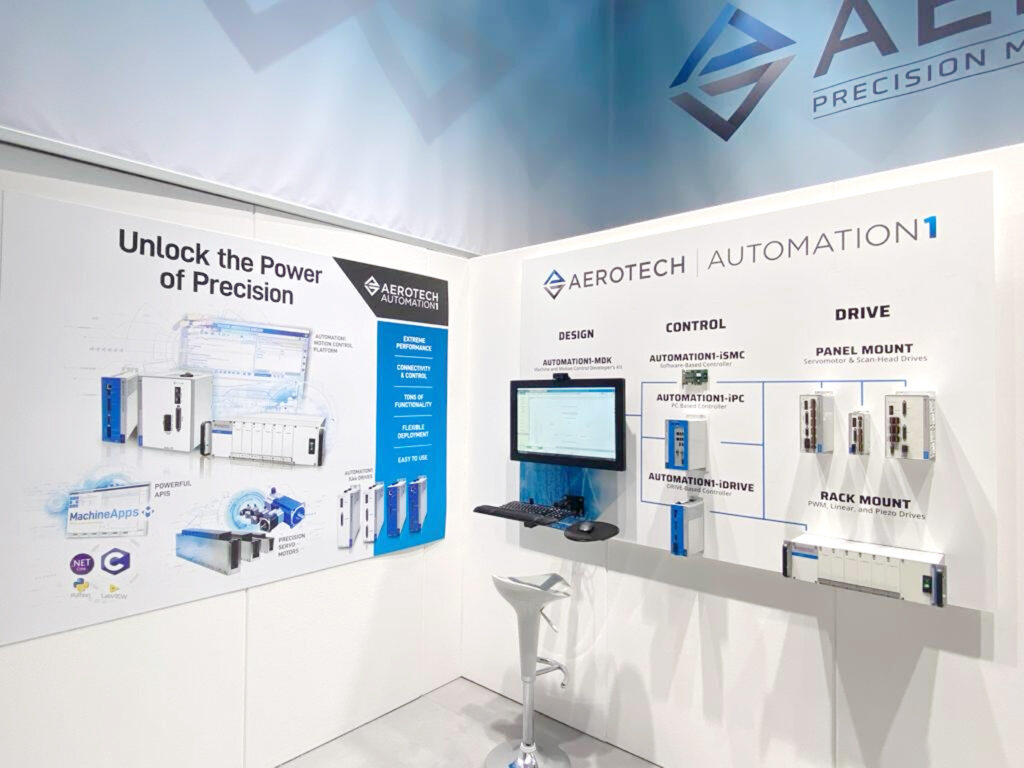
Camera module integrated in motion control: A camera recording is used as a live video feed with optional crosshairs as well as the capture and display of images and axis positions are displayed directly on the screen of the control platform in order to monitor the production process, for example.
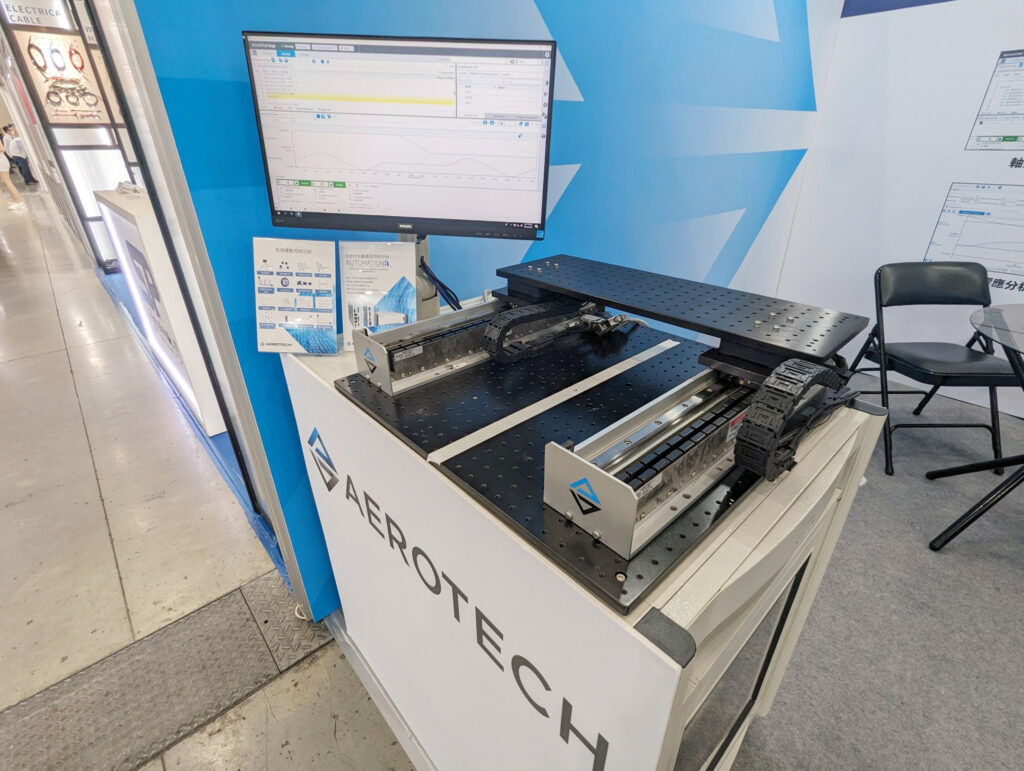
The decoupling control in Automation1 can also be used to control a rotary movement
(yaw) on the yaw axis (theta) when working with a flexible gantry.

Specially developed for use with the Automations1 motion control platform: the new
digital PWM drives XA4 and iXA4