Aerotech supplements Automation1 with a variety of innovative functions for machine builders too.
Aerotech have further expanded their Automation1 motion control platform: The latest version 2.8 comes up with a customisable CNC user interface and, according to the manufacturer, now offers even more flexibility and user-friendliness for CNC users.
“Our users have been eagerly awaiting this release of software which adds support for the new 4-axis version of the XA4 series controller allowing control of 4-axes within 1 box” says Simon Smith, European Director at Aerotech. “Of course, the software developers in Pittsburgh always try to respond to current customer requirements and incorporate them into the next release of Automation1.” An extended DC power supply (100 VDC) and the EB1 and EB2 I/O expansion boards have also been added giving the user much higher levels of flexibility. In addition, the control platform now supports the setup wizard for linear gantries. These can be configured flexibly in the machine setup and offers users even greater customisation options.
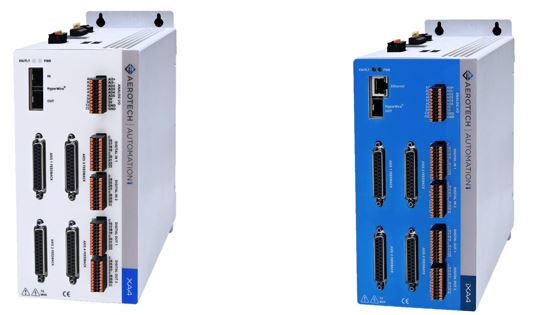
XA4 and iXA4-PWM drives now available with 4-axis expansion card for Automation1
Optimised data acquisition and program interface
Presettings for data acquisition are now also possible in the motion control platform. These can then be saved as predefined configurations in the control units. This saves time and also allows the user to switch quickly and easily between the presets. The various help files have also been improved and expanded to include a more user-friendly structured interface. Users can now navigate directly to the stored hardware manuals as well as to additional sections for data acquisition and movement optimisation.
New tools for CNC machine builders
CNC machine builders have an extended range of tools at their disposal, including the ability to create customised T-codes for specific Aeroscript routines. In addition, Automation1 now has tools to compensate for cutting tools and workpiece offsets. They compensate the X, Y and Z offsets of a cutting tool or programme movement relative to a fixed point. This significantly improves the precision and quality of cutting processes. “Together with the official release of user-defined modules, INI file support and 3D visualisation, Automation1 is now better equipped than ever before,” specifies Daniel Hong, Controls Product Manager at Aerotech.
With the integration of INI files, machine and tool positions as well as process setpoints can be saved and retrieved, which improves the organisation and management of machine parameters. New array variables improve communication within programmes and make programming more flexible and efficient.
Customised CNC interfaces
In Automation1, CNC interfaces can be customised with new functions such as feedhold, retrace and manual feed override. CNC users can also create their own modules with .NET and improve the visualisation of data. Optimisations in the user interface and controller functions offer more functionality and user-friendliness. The extended help pages make it easier to access important information and support resources.
Never lose the overview
In addition, 3D data signals can be configured and displayed in the Data Visualizer module, allowing for more detailed visualisation and analysis of motion data. Presets enable data acquisition for predefined configurations for data acquisition that are stored in your control unit. This saves the user time as they can quickly and easily switch between presets.
The Automation1 help files have been further improved with a restructured homepage. Navigation to the hardware manuals has been added to the homepage. A new “Data acquisition and controller status” and “Motion” section has also been added to cover Automation1’s wide range of data acquisition and motion enhancement tools.
Controls Product Manager Daniel Hong concludes: “Automation1 is becoming increasingly flexible and powerful without compromising on user-friendliness. Version 2.8 provides users with important tools to quickly and easily develop and deploy an HMI, especially for CNC operators.”
Aerotech Ltd