Aldershot-based Ultrasonic Sciences Limited (USL) are specialists in the design and manufacture of bespoke automated Non-Destructive Testing (NDT) inspection systems. USL has supplied industry with automated inspection systems and PC-based instrumentation for 40 years and, during this time, thousands of machines have been installed globally supporting a wide range of applications.
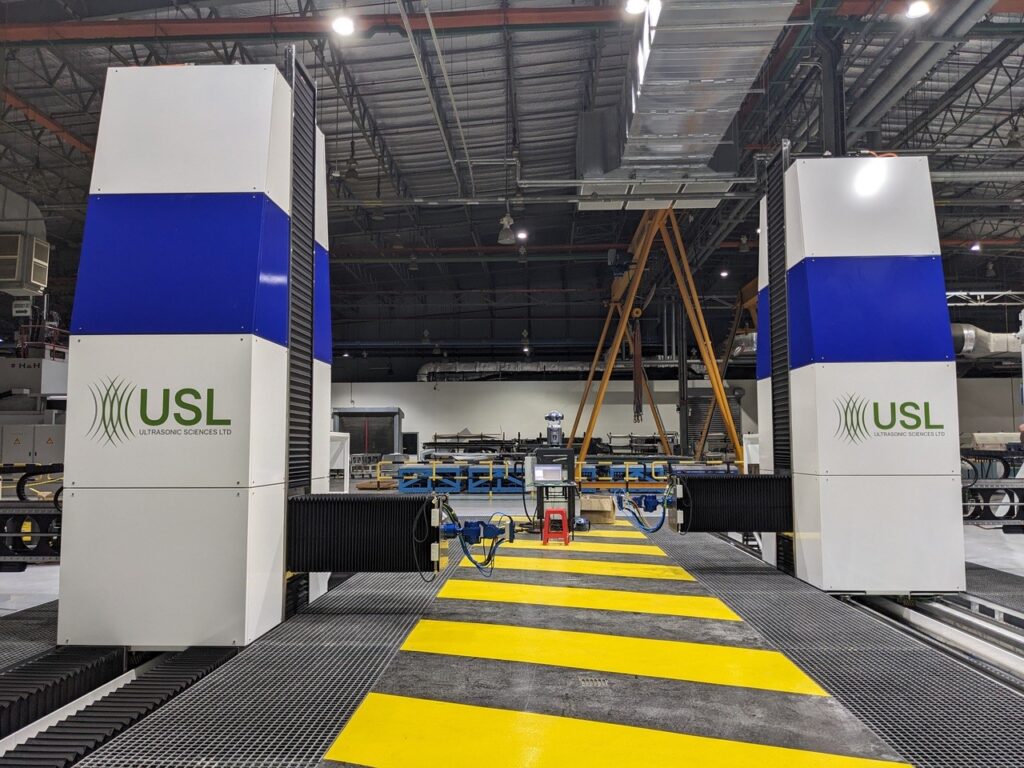
The 25-strong company supplies advanced ultrasonic NDT systems and services to a wide range of industries across the world including aerospace, automotive, energy, rail, raw material production and manufacturing. Its bespoke inspection solutions serve customers focused on high-precision quality control and material integrity analysis.
Sourcing suppliers who understand the nature of USL’s work, especially the level of customisation between each machine, and being able to work together to implement the best possible solution became a real challenge for Niko Bayer, Technical Sales Manager for USL, during the pandemic. It was then when he discovered STOBER. He contacted Martin Preece, Head of UK Subsidiary, to discuss lead times at STOBER and discovered they were significantly faster. This was exactly what he needed to support USL’s delivery of a significant aerospace contract.
The Project
Niko and his colleagues were tasked with designing, building and installing a 12-axis dual tower machine and 11-axis gantry machine for inspection of composite components for a long-standing aerospace client.
Explains Niko: “Custom-built machines such as these are preferred to standard ‘off-the-shelf’ designs due to being an exact fit for requirements, flexibility and scalability, their enhanced accuracy and performance and specialised capabilities.
“For all our automated inspection machines, key considerations for motion related components such as motors, are precision and accuracy, resolution, speed control, torque, load capacity, closed loop control, communication interface, safety features and longevity. Mechanical systems for automated ultrasonic inspection machines are often subject to long use periods, repetitive motion and regular changes of direction, often in humid environments.”
Continues Niko: “After discussing our requirements with Martin, we were more than confident that we could get the range of choice, precision and accuracy, quality and reliability we need to build market-leading machines from STOBER.
What’s special about the machine?
This particular system called for dual sided machines for simultaneous through transmission and pulse echo (both sides) inspection of aerospace composite components. With large scan areas and a range of specialised end effectors, inspection of large components with complex shapes, including leading edges and flap track fairings and thick sandwich construction parts, are able to be comprehensively inspected while meeting all the rigorous mechanical accuracy and ultrasonic requirements of the end user.
Where is the machine being used?
All manufacturers of composite components and structures for use in aerospace applications require inspection to ensure finished parts are free of defects. As aircraft manufacturers push to increase efficiency, save weight and cost, the amount of composite materials used in aircraft construction has increased significantly. As manufacturing techniques evolve, composite parts are becoming larger and more complex requiring larger and more capable inspection equipment.
The STOBER solution
“In order to fulfil the project’s specific and exacting requirements, a number of STOBER components were discussed and consequently specified following several technical meetings with Niko and the USL team,” explains Martin Preece.
The Drive System Solutions provided offered a seamless integration right from the Servo Amplifier to the Rack and Pinion Gears. The solutions included:
· Linear and Rotary Axes for Systems:
o Various Servo Motor sizes from the EZ range offering Super compact, maximum torque combined with high dynamics
o Latest Generation Servo Drive Amplifiers from the SC6 range
o Variety of Servo Gearbox technologies selected for stiffness and precision
o OCS – One Cable Solution for all Motors capable of up to 100 metres
Continues Martin: “Our motors and amplifiers were sized and selected in conjunction with USL to optimise performance depending on the drive transmission either rack and pinion, ballscrew or direct drive depending on the specific requirements. Niko and his team often employ a combination of these for different axes on the same machine to achieve the precision, accuracy and reliability demanded.”
The benefits of working with STOBER
“Over the years, we have used many different motors and amplifiers from various suppliers,” outlines Niko. “With STOBER, we get the range of choice, precision and accuracy, quality and reliability we need to build market-leading machines.
“Another major benefit of working with STOBER is lead time and availability the company can provide. In our experience, it has had consistently shorter lead times and better on-time delivery than others.”
Continues Niko: “One feature we had with previous motors was the ability to implement friction feed forward values above 100%. By anticipating and counteracting the effects of friction, systems with this feature can achieve smoother, more accurate motion especially in applications that require precise positioning. On discussing this, STOBER were happy to implement our requirements into the SC6 amplifiers to allow this feed forward value up to 200% which afforded us the ability to tune our machine axes for exceptional positioning.
“Furthermore, STOBER supply Integrated Geared Servo motors without a motor adapter thus aiding easier installation due to its compact design, Lower weight but increased power density. The team is also very helpful when specifying machines, assisting with speed, torque and load calculations. Single cable solution lengths allow more freedom when designing larger machines.”
In conclusion
Both machines have now been installed and commissioned at a facility inspecting Boeing aircraft structures and components, having exceeded all mechanical accuracy requirements.
“All of us at USL are very pleased with STOBER products and how they perform as a core component of our machines,” states Niko.
“We appreciate the solution-oriented approach to finding tailored solutions that best fit our highly technical systems. USL has been able to enhance the performance and reliability of our systems while streamlining the design and build process. Overall, the synergy between USL’s extensive industry expertise and STOBER’s motion control solutions has led to the successful implementation of cutting-edge technologies, meeting the evolving demands of the aerospace sector.”
A special thanks
Adds Niko: “We would like to extend a special mention to Martin for his exceptional support throughout the collaboration. Martin was proactive, helpful, and a pleasure to deal with, ensuring that USL received the guidance and assistance needed during the entire machine build and delivery process.
“His commitment to understanding our requirements and addressing our challenges made a significant difference in the project’s success. STOBER’S dedication and expertise were invaluable in facilitating a seamless integration of their system solutions into our automated ultrasonic inspection systems, contributing greatly to the overall efficiency and effectiveness of our operations.”