RTEC Engineering Ltd, a UK-based contract engineering services company near Mansfield in Nottinghamshire, is on a mission to redefine accuracy standards for dynamometers amid the growing global interest in enhancing engine efficiency and performance. Their cutting-edge technology is grounded in a novel torque measuring technology, also of British origin.
Rob Langton, the Managing Director of RTEC Engineering Ltd and an engineering metrologist with over two decades of experience, sheds light on their innovative approach: “Our sub-division, RTEC Powertrain, is actively engaged in collaborative projects with B2B partners, concentrating on metrology solutions for the automotive industry, including ECM (engine control module) calibration and diagnostics.”
Facing the challenge of obtaining a detailed performance profile for a specific engine within a constrained capital budget, Langton took matters into his own hands. Drawing on his extensive engineering expertise, he embarked on designing and manufacturing a dynamometer that replicates the accuracy and reliability of OEM or lab-grade systems but at a more accessible cost for small to medium-sized enterprises.
Striving to surpass the limitations of load cells and RPM sensors commonly found in traditional dynamometers, Langton turned to advanced technology. After researching specialized literature, he discovered Sensor Technology in Banbury and their non-contact TorqSense transducer.
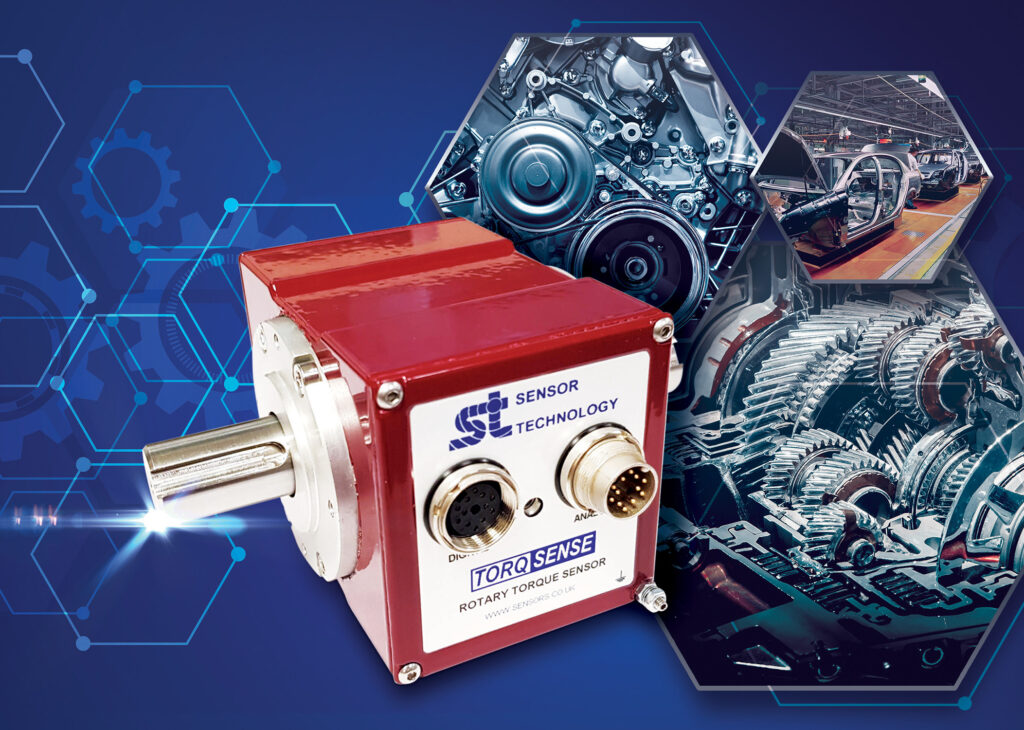
Engineers from Sensor Technology assessed Langton’s requirements and recommended the SGR510/520 series TorqSense. This innovative transducer employs a full four-element strain gauge bridge. A rotor-mounted ultra-miniature microcontroller, powered by a non-contact inductive coil, measures strain values and transmits them digitally to the stator, providing high-precision torque measurements.
Langton highlights the benefits: “The inductive coils eliminate the need for wires with slip ring connections to the shaft, offering the ease of use we desire.” He underscores TorqSense’s remarkable 250% overrange capacity, enabling accurate measurement of sudden load spikes. Additionally, its immunity to noise and signal corruption, common in slip ring setups, along with a 4000/sec sampling rate, aligns seamlessly with their resolution requirements.
With Sensor Technology’s assistance, RTEC swiftly developed an ideal solution for manufacturing a high-performance dynamometer aligned with their design specifications. Recognizing the potential broader applications, Langton explored the market’s needs, leading to a realization of a gap that RTEC aims to fill.
While calibration of elements like the load cell is typically carried out by UKAS accredited laboratories in larger organizations, RTEC identified a market gap for smaller entities. They are now working on a scalable, modular dynamometer design with TorqSense at its core. TorqSense’s factory calibration to NPL standards and its self-contained nature, combined with a plug-and-play design, simplify exchanges during calibration, minimizing downtime.
RTEC’s future projects include crafting bespoke test rigs tailored to users’ exact specifications and retrofitting TorqSense into existing dynamometers and test rigs, spanning precision instrument drives to heavy vehicle power trains.