Lightweight materials used in F1 design unlock opportunities to boost sustainability
A new demonstrator vehicle showcasing cutting-edge design and manufacturing innovation for space will be unveiled by the National Manufacturing Institute Scotland (NMIS) today (11 March) as part of Space-Comm Expo – the UK’s largest space industry event.
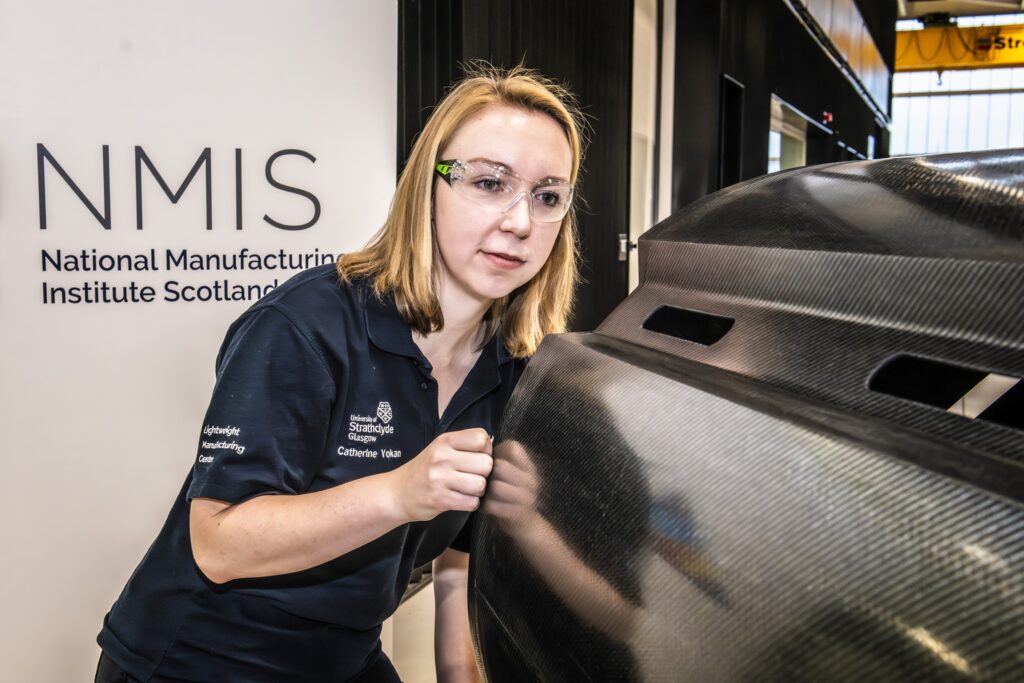
Catherine Yokan of the LMC
Designed by the Lightweight Manufacturing Centre (LMC) at NMIS – which is operated by the University of Strathclyde and part of the High Value Manufacturing (HVM) Catapult – the space vehicle brings together bold ideas for future manufacturing, highlighting possibilities that could be used for future launches.
A concentric liquid oxygen (LOX) and propellant tank will be on display, which is just one part of the centre’s overall concept. Along with the use of lightweight advanced composite materials and digital and additive manufacturing techniques, a core component of the second-stage design is its recoverability, with technology to enable a controlled de-orbit and return to Earth.
The concept has been developed as part of the Stratelite Space and Photonics project, which is part-funded by the Glasgow City Region Innovation Accelerator programme led by Innovate UK on behalf of UK Research and Innovation.
Scotland is already at the forefront of space innovation, with Europe’s only fully licensed vertical launch spaceport, SaxaVord in Shetland, preparing for its inaugural orbital launch later this year. NMIS’s technical capabilities in next-generation manufacturing, materials and skills development mean the centre is well placed to support the growing sector with future developments.
The demonstrator builds on the work NMIS is already doing in the space market, supporting local companies and global players with solutions to some of their most complex manufacturing challenges. According to Space Scotland, the sector contributes more than £4 billion to the economy per year , with almost one-fifth of all UK jobs in the sector based in Scotland .
Professor Iain Bomphray, director of the LMC, said: “It is a particularly exciting time to be working in Scotland’s space sector, with the first launch on the horizon unlocking significant opportunities for the burgeoning ecosystem and space technology companies based here. NMIS has already been involved in a range of projects, but our new demonstrator brings all of that together, showcasing capabilities at full scale and taking a fresh approach to design and manufacturing for space with a specific focus on composites.
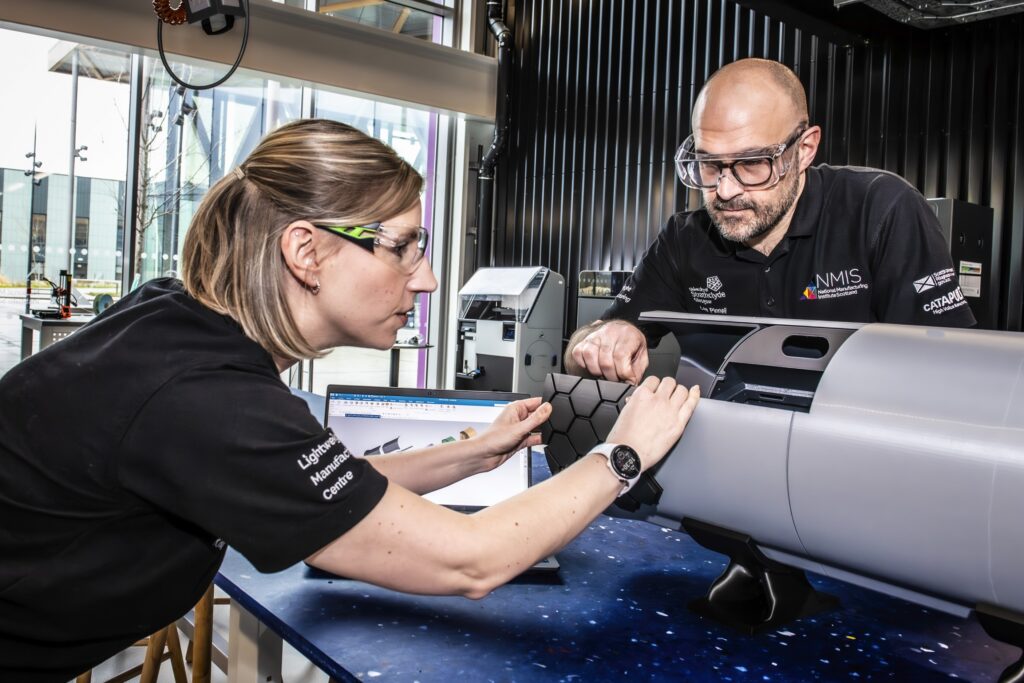
Kirsty Pinnell and Lee Pinnell of the LMC
“The space sector here is still in its infancy, and we need to nurture the high-growth potential startups and spinouts that are paving the way. That is where NMIS comes in, we want to support businesses to succeed through collaboration and access to expertise, research, manufacturing facilities and testing capabilities. We intend to seed new companies and play a part in growing the ecosystem.
“An understanding of the industry and its challenges underpins our capabilities and the design for the concept. The economics of space are changing, and companies are placing a greater emphasis on sustainability than ever before. That starts on the ground, with reusable designs, efficient manufacturing, ways to reduce waste, eliminate space debris and build a greener space economy.”
In a typical multistage rocket, the first stage is designed to propel the vehicle upwards, while the second stage is responsible for accelerating the payload to its final orbital velocity. SpaceX was the first to successfully recover a first-stage space vehicle in 2015, rather than designing it to burn on re-entry. However, second stages are not yet recoverable in the same way, with the remains typically staying in orbit.
Extra elements required for re-entry and landing – such as heat shields, deceleration mechanisms and stability systems – can add significant weight to a space vehicle, but the design of the demonstrator is an example of how NMIS is challenging convention and pushing boundaries to showcase its capabilities as a research partner.
Iain added: “Using novel composite materials, we can aim to make space vehicles lighter to offset additional functionality and maintain payload capacity. Steel and aluminium have been the most widely used materials so far, but drawing upon techniques used in the construction of F1 cars, we have explored new ways to integrate composites into spacecraft design. A recoverable second stage could enable spacecraft to make better use of the energy expended in reaching orbit, allowing for additional functions such as satellite servicing before re-entry.”
NMIS’s space demonstrator will be on display at Space-Comm Expo at ExCeL London from 11-12 March. For more info, visit: https://www.nmis.scot/