According to the International Society of Automation, factories worldwide lose 5-20% of their productive capacity to unplanned downtime. With supply chain disruptions increasing, Mitsubishi Electric’s predictive maintenance solutions help manufacturers identify equipment failures before they occur, maintaining operational continuity.
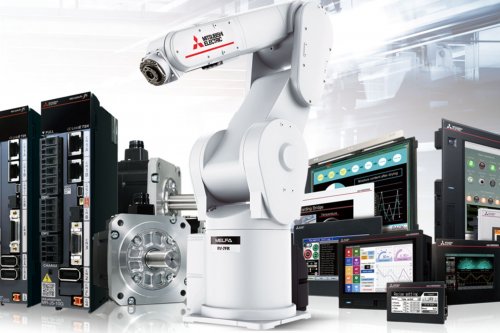
Mitsubishi Electric Predictive Maintenance Solutions
Research from Arimo shows the average plant loses 15 hours weekly to downtime, with production lines facing approximately 20,000 interruptions annually. According to Resilinc, manufacturing disruptions increased by 30% in the first half of 2024 compared to last year, with factory-specific issues rising by 40%.
Higher transport costs and worker shortages have amplified the impact of each stoppage. In this environment, predicting maintenance needs gives companies a significant advantage. Mainly due to the early indication of a fault, allowing it to be fixed during the next maintenance period, which means longer machine uptime.
AI-Maintenance In Figures
“When we can spot equipment failures weeks before they happen, the whole supply chain benefits,” explains Daniel Sperlich, Strategic Product Manager Controllers at Mitsubishi Electric Europe. “We can order spare parts for repair that can be stored until the next planned maintenance phase. And, we allow the production line to continuously run, without any interruptions – including those caused by a lack of spare parts when these are needed ‘here and now’ . “
As Rafi Ezra, Managing Partner US Industrial Market at IBM Services states: “AI-powered maintenance solutions can cut downtime by up to 50%, reduce breakdowns by 70%, and lower overall costs by 25%.”
Industry Response to The Needs
Mitsubishi Electric has developed several predictive maintenance systems. Their MELFA FR series robots with Smart Plus cards track performance and identify potential issues early. The company’s MELSERVO-J5 servo amplifiers use AI to detect wear in critical mechanical parts by analysing vibration patterns, tension changes or backlash. Additionally, the FR-E800 Series inverters feature Corrosion Alert System and Life Diagnostics Function to monitor component conditions.
“Today, implementing predictive maintenance tools is no longer just an advantage but a necessity for companies that want to stay competitive,” emphasises Daniel Sperlich, Strategic Product Manager Controllers from Mitsubishi Electric. “Our solutions help manufacturers address problems before they affect their production lines. We ‘put intelligence’ where it is required most, directly into our equipment, close to the mechanics.”
Real-World Impact
At Mitsubishi HiTec Paper Europe GmbH, a monitoring system for cooling fans in a paper machine paid for itself in just one hour of production time. With daily production exceeding 300,000 kg, preventing even brief stoppages brings significant financial benefits.
“Supply chain reliability starts on the factory floor,” says Daniel Sperlich. “When a machine can self-diagnose before breaking down, it prevents the chain reaction of missed deliveries that can disrupt downstream operations.”
The Predictive Future
The global predictive maintenance market, valued at $7.85 billion in 2022, is expected to grow at 29.5% yearly through 2030. “There is growing interest in implementing new maintenance systems step by step to optimise productivity. The idea here is that improvements can start at the machine level as well as the whole line or factory level so that automation is perfectly tailored to meet the specific needs of a particular production facility” – adds Daniel Sperlich. “In this way, the return on investment is also much easier to calculate and fully understand. At Mitsubishi Electric we call it the Smart Manufacturing Kaizen Level (SMKL) approach”.
The dynamic growth of the predictive maintenance market reflects the increasing need of manufacturing companies to shift from reactive to proactive strategies, enhancing performance whilst stabilising supply chains in uncertain times. A key driver is the ability to implement these solutions in a scalable manner—from individual devices to entire production facilities—without requiring significant initial capital investment and with clear and easy ROI calculation.