The adoption of collaborative robots, across multiple sectors, continues at a pace as
increasing numbers of manufacturers realise the potential these robots have to provide a
cost effective and productive solution to a wide range of applications. Designed specifically
to be able to work safely alongside humans, collaborative robots generally feature an
aesthetically pleasing smooth rounded design, with no sharp edges which could cause injury
if the robot accidentally comes into contact with an operator during its cycle. In addition, the
arm joints are usually encapsulated to ensure that there are no pinch or trap points for
human fingers or hands.

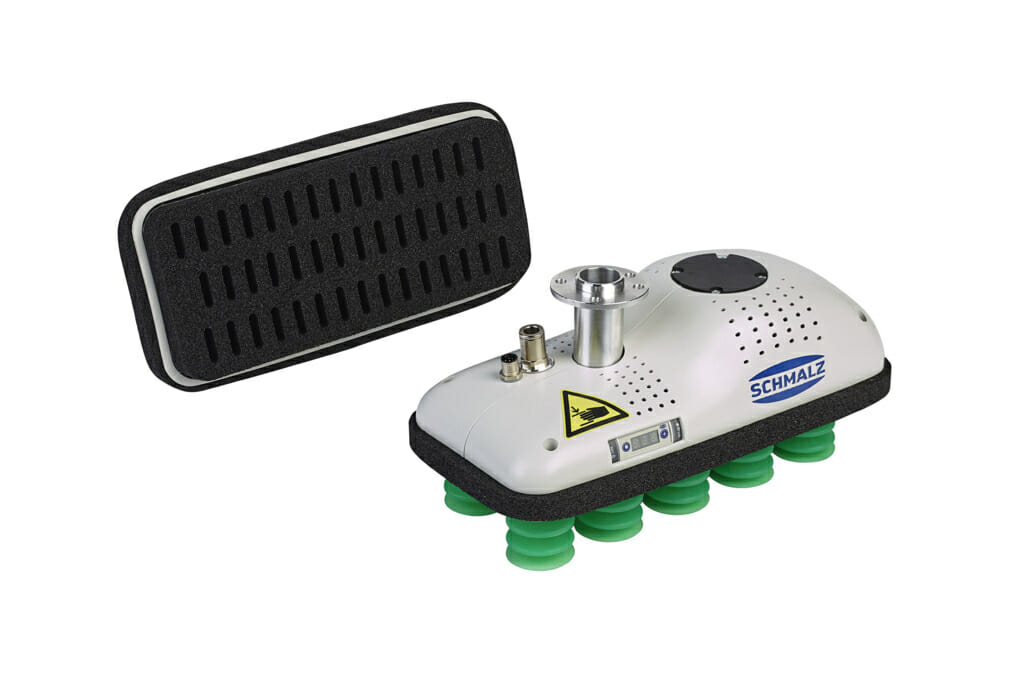
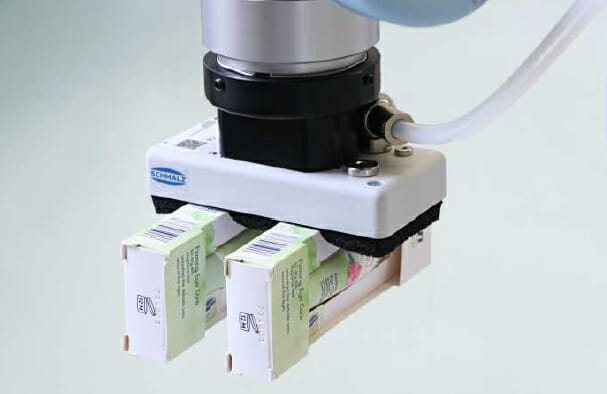
Just as these robots have evolved in recent years to provide greater reach and payload
capabilities, so too have the gripper technologies they use, not only to cater for the wider
range of applications where these robots are being applied, but also to ensure that the
gripper design and functionality complies with ISO TS 15066, which provides guidance for
collaborative robot use. In addition, to maximise the Cobot’s potential for operational
performance and flexibility, the gripper systems themselves need to exhibit characteristics
which promote ease of integration and use across a diverse range of applications.
Collaborative Vacuum Gripper Technology There has been a significant uptake in the use of
collaborative robots for product handling, palletising, and de-palletising applications in recent
years. This has been the catalyst for the development by Schmalz of a comprehensive
range of gripper systems targeted at collaborative robot applications.
To maximise the performance and payload capabilities of the collaborative robot, the weight
of the gripper system should be optimised and, in keeping with the ease-of-use concept
promoted by suppliers of collaborative robots, ideally the pneumatic vacuum generation
technology should be integrated within the gripper unit to simplify integration and operation.
New additions to the Schmalz range include the FXCB / FMCB area grippers, which are
designed to support handling tasks with collaborative robots. These gripper systems will be a
valuable asset for a wide range of applications within intralogistics, such as end-of-line
packaging, and pick-and-place applications. The innovative design of these gripper systems,
which uses 3D printing as part of the manufacturing process, complies with ISO TS 15066, and the FXCB variant also includes integrated vacuum generation. Additional features of this range include innovative communication technology via IO-Link, and an integrated
NFC (near field communications) chip. The Schmalz FQE range also offers flexible handling of workpieces, regardless of size and geometry from different pick-up positions. Also designed for use with collaborative robots, these gripper systems provide solutions to handling applications across multiple sectors
such as the automotive, glass or electronics industry, in addition to end of line packaging
and intralogistics tasks. The “X-variant” of this area gripping system comes compete with a particularly energy- efficient, fully integrated pneumatic vacuum generation system, with the alternative “M
variant” designed for operation with an external vacuum generator. With their low weight
and low noise levels, together with their smooth rounded design, these grippers are also
suitable for human–robot–collaboration applications, meeting the ISO TS 15066 standard.
Enhancing Collaborative Robot Operation
The design of these gripper systems from Schmalz promotes and supports the safe
environment requirements for employees when working alongside collaborative robots. In
addition, the low weight and dynamic geometry of these compact and energy efficient grippers,
ensure optimum operational robot cycles, whilst the process and condition analysis functionality which is also available, provides useful information for maintenance personnel and which can be accessed using a smart-phone.
For more information visit our website – www.schmalz.com