Contactless measurement of liquids and solids has taken a leap forward with SICK’s new LXRC and LXRH sensors. Designed specifically for continuous level monitoring and using free-space radar technology, the devices are accurate, repeatable and suitable for an enormous range of applications across many sectors and industrial environments within factory and process automation.
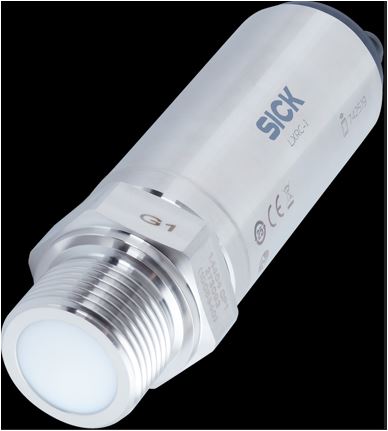
Using frequency modulated continuous wave (FMCW) radar, the LXRC and LXRH sensors can measure levels of liquids and bulk materials up to 15 m, with an accuracy of +/- 2 mm, providing ideal, easy installation solutions throughout industrial operations. For example, the LXRC, and the LXRH (which comes with hygiene adaptors), can be used at any stage of a dairy operation, from milking to packaging.
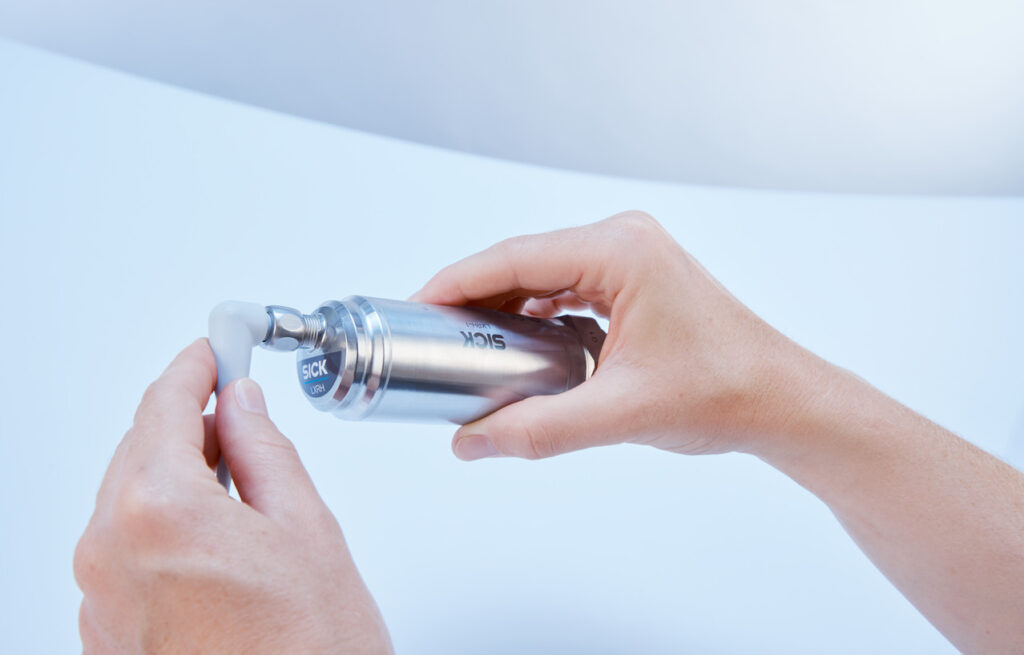
Solving the problems of level measurement
Because the sensors use contactless FMCW radar technology, both the LXRC and LXRH overcome a range of problems associated with alternative level measurement techniques. Contact measurement technologies can require increased effort to clean tanks and sensors, sustain damage from abrasive, highly viscose or aggressive materials, and see build up on the sensor probe affect measurement.
In addition, challenges associated with Ultrasonic measurement include vacuum, dust, condensation, steam, temperature or build up affecting readings, and limited “windows” of usable distance. With free-space radar all these problems are eliminated as there is no contact and there are no dead zones.
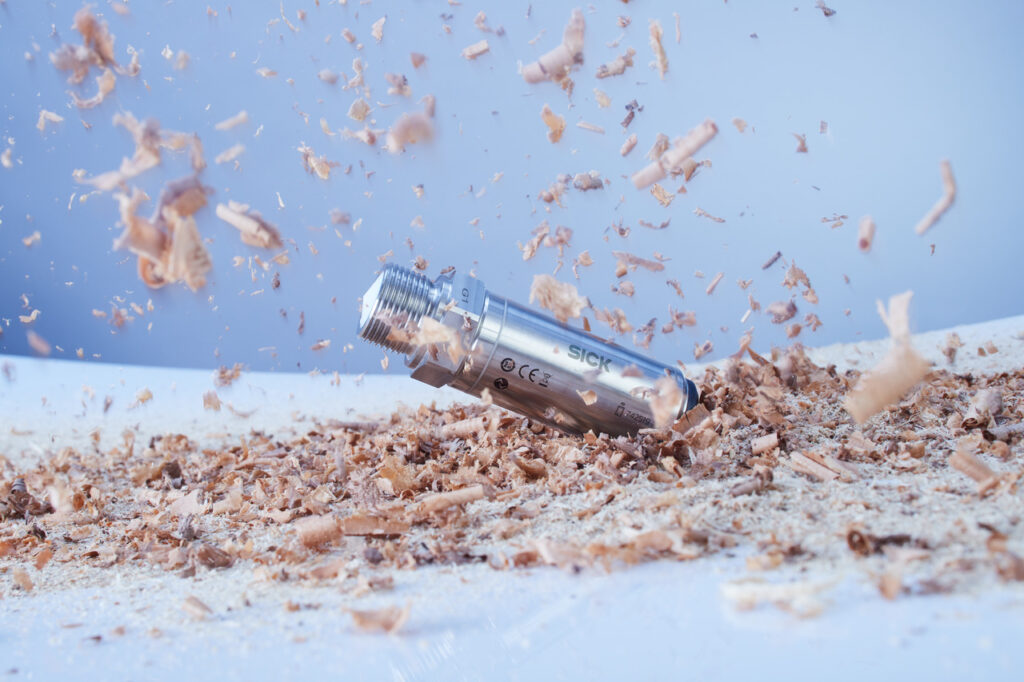
Accurate and repeatable measurement without limits
Free-space radar technology is accurate and repeatable. It can be used in an almost limitless range of applications; from water and wastewater treatment to dairy processes and paper pulping, and from transfer of aggregates and hydraulic power packs to moving expensive chemicals around a factory and pharmaceuticals.
The LXRC and LXRH sensors can be used throughout industrial processes and easily fitted to a huge variety of machines and containers for the measurement of almost all bulk materials and liquids. This means just a single item for inventory and maintenance across an array of process application conditions.
A one for all solution for anything that is continuously measured and controlled, the LXRC solution is suitable for most factory automation and industrial applications. Meanwhile, the LXRH provides the same high performance but with hygiene adaptors, conforming to industry standards and sanitary requirements for industries such as food & beverage, dairy and pharmaceuticals.
Robust and equipped for the future
Complete with mechanical process connections and communications capabilities, the compact 80 GHz LXRC and LXRH free space radar level sensors with IO-Link come with standard analogue and digital outputs and are Industry 4.0 compatible. They are available with optional Bluetooth connectivity for easy commissioning and diagnostics on a tablet or smartphone via the SICK app.
The impressive range of up to 15 m is suitable for large tanks and silos, while the devices are highly accurate to +/- 2 mm. An operating temperature range from -40 °C to 130 °C and process pressure range from -1 bar to 16 bar make the LXRC and LXRH sensors suitable for use in harsh environments.
Complete with eye height status indication, both devices have short lead times and come with SICK’s expert support and dependable quality. SICK’s experienced teams work closely with customers to solve their application problems with the best possible solution from the company’s huge portfolio of sensing technology.
Nick Hartley, SICK UK Market Product Manager – Instrumentation & Distance Measurement, says, “Sensors are the unsung heroes when it comes to material handling and transfer. The LXRC and LXRH sensors solve a range of industry challenges associated with contact and Ultrasonic technology and can be used on almost anything continuously measured and controlled. They perform strongly in harsh environments and throughout multiple operations, providing a single solution to meet many customer needs.
“We are delighted to offer a hi-tech solution for factory automation that provides high accuracy and repeatability, with commissioning and maintenance reduced to a minimum.”