Aircraft landing gear has critical engineering requirements due to the demanding and varied forces it must withstand during take-off, landing and ground operations. Regarded as a ‘mechanical marvel’ by some aviation experts, it is certainly a big deal with the world’s top airline manufacturers considering the fact that it accounts for around 20% of total aircraft maintenance and around 7% of the total weight of today’s commercial aircraft.
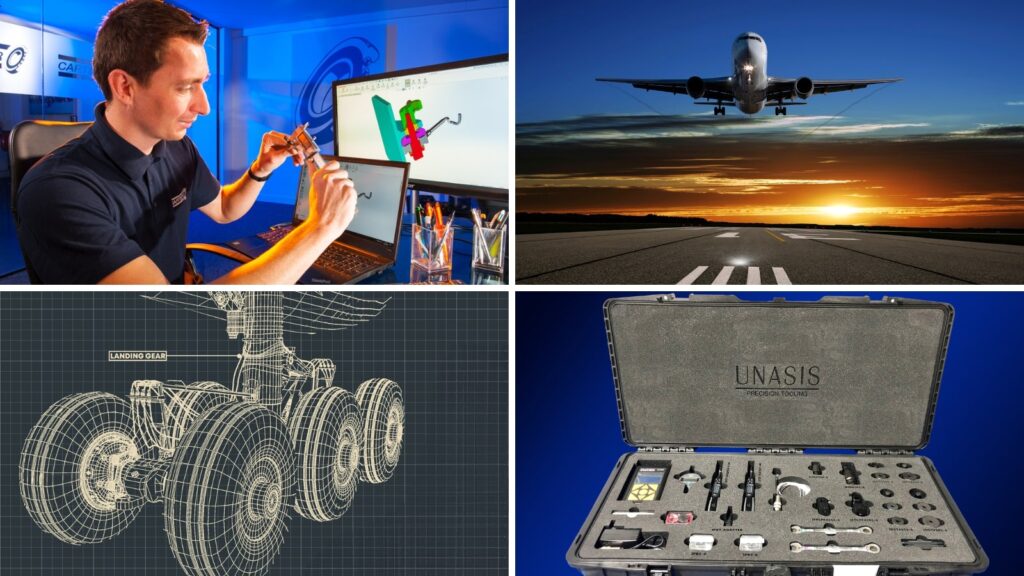
Aircraft Landing Gear – The Facts
When an aircraft lands, the landing gear has to absorb the entire weight of the aircraft, which can range from around 64,500kg for an Airbus A320 and up to around 201,800kg for a Boeing 777. Clearly the landing gear must be robust enough to handle not only the vertical load, but also the horizontal forces generated by the forward motion of the aircraft. Additionally, during landing, the gear must absorb the impact energy which can be substantial, especially during hard or emergency landings. Therefore, the key requirements demand designs and materials that can dissipate energy effectively, while avoiding structural failure.
Specialist Suppliers – Ensuring Maximum Efficiency and Safety
Today landing gear is typically manufactured by specialist suppliers to the aviation industry, who then supply to the major aircraft manufacturers. This is because the landing gear and shock absorption technologies are recognised as specialist, separate fields of science when compared to other aspects of aviation technology. Beyond impact absorption landing gear must also provide optimum stability and control on the ground as aircraft often encounter varying ground conditions, including uneven and slippery surfaces and crosswinds. The design must ensure that the aircraft maintains directional control during taxiing, take-off and landing, even under adverse weather conditions.
Meeting the Challenges
To achieve this today’s landing gear systems incorporate features such as shock absorbers, anti-skid braking systems and steering mechanisms.
These components must work together seamlessly to prevent the aircraft from veering off the runway or skidding, ensuring passenger safety whilst minimising wear on the aircraft’s tyres and other components. The landing gear must also be designed with considerations for weight and space constraints because fuel efficiency as part of overall aircraft performance, has never been more important than it is today. Therefore, the landing gear must be lightweight yet strong, utilising advanced materials such as titanium alloys, or high strength composites. Also the landing gear must be retractable to reduce aerodynamic drag during flight which means complex mechanical systems are needed to ensure reliable extension and retraction. Balancing these requirements; strength, stability and weight efficiency, while also integrating the landing gear into the aircraft’s overall design, makes it one of the most challenging aspects of aircraft engineering.
Precision Bearings and Tooling Equipment – Essential Components
Specialist bearings are an essential component of innovative landing gear systems particularly when applications involve landing gear struts and actuators and precision bearing and tooling specialists CARTER MANUFACTURING are approved aerospace bearing suppliers to industry leading landing gear manufacturers. Carter’s key focus is high quality and customer satisfaction illustrated by the accreditations to ISO9001, incorporating the requirements of AS9120, with flow down to AS9100. Carter also specialises in the custom design and manufacture of Aerospace Bearing Tools, because your application could have clearance restrictions, such as blocker door, or flight control MRO repair. Or maybe you’d like to streamline your production with a custom tooling package and Carter has an impressive back catalogue of thousands of proven custom tool designs and world-class tooling engineers ready to design innovative, bespoke solutions for any application.
Carter’s swaging tools are precision engineered to fit specific landing gear bearings, reducing operational risks and costs by reducing the likelihood of damaging expensive bearings and housings. When a specific application requires a different approach, or the customer doesn’t wish to use portable tools, the drill press style swaging tools are a much better alternative to anvil staking tools. This is because the required swaging force is just a fraction of the overall staking force and will significantly improve the quality of the swage.
Finally, Carter also offer a comprehensive range of tool training services and technical support ranging from trouble-shooting to multi-day training packages. This means that every one of our customers can rest assured they will have the necessary skills required to utilise our tools to the highest performance standards. Bearings.