The concept of preventative or predictive maintenance is not new and has been a key factor in ensuring reliable plant operation and optimum productivity levels for many years. What has changed over time however is the methods and technologies used, which today make it possible to monitor production assets in real time. The ability to interrogate equipment and measure performance allows for more accurate predictions of where and when production technologies are likely to require attention, helping to avoid unnecessary breakdowns.
Stäubli’s Simon Jenkins looks at the latest developments from Stäubli and explains the benefits which their new SCOPE system will bring to the users of the company’s robot systems. By analysing robot health and stress on the fly, it produces notifications on upcoming maintenance, therefore offering an overview of production assets and delivering better control of overall equipment efficiency (OEE).
SCOPE is Stäubli’s secure solution for continuous EDGE data mining. EDGE data is data that is obtained as a result of edge computing processes, performed at or near the physical location of the source of the data, in this case the customer’s robot fleet.
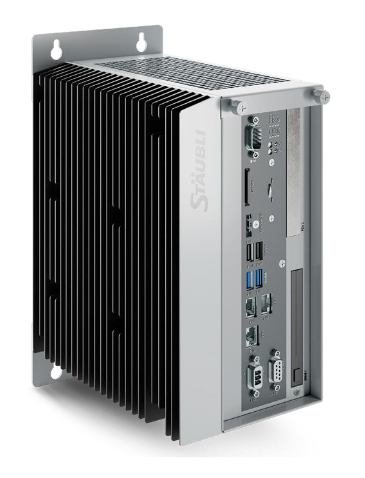
As solution to monitor, review and analyse production, plus optimise automation and maintenance processes, SCOPE makes it possible to anticipate breakdowns and move closer to achieving the ultimate objective of zero downtime. SCOPE integrates the latest Stäubli Technologies, improving the performance of production processes and extending the lifetime of the users’ robot fleet within a single platform.
As a decentralized EDGE solution, SCOPE ensures that users retain ownership of their data. Stäubli’s open data routing functionalities, via HTTP, WebSocket or MQTT, offer full connectivity to any compatible MES (manufacturing execution system) or ERP (resource planning) layers for further local investigation or informative tasks such as E-Mail or SMS notifications.
Who Needs Data?
In a world where Industry 4.0, the IOT and AI are becoming an integral, and increasingly essential part of manufacturing, the ability to acquire and interrogate data has never been more important. For machine builders and system integrators the data provided by SCOPE will aid in optimising robot trajectories, cycle times, and robot lifespan, by providing notifications of early signs of failure, enhancing troubleshooting processes, and avoiding unnecessary downtime. Once in production, end users can use data to help stabilise their production process, production quality, and to detect early signs of any process related issues. From Staubli’s perspective the data acquired by SCOPE is a valuable asset when it comes to training models and moving towards predictive maintenance solutions that will continuously improve the lifespan of the robot. In practice, data generated by the robot is recorded and sent to SCOPE 250 times per second. This data is then analysed, and SCOPE produces an easy-to-understand report. Analysis results are logged to create timelines and trend charts on the SCOPE dashboard. In the event of deviation in the results produced, SCOPE can be programmed to send alerts to existing MES or ERP software solutions. With the capability to connect to and monitor up to 50 robots, users are able to view and interrogate status through a series of intuitive dashboard displays.
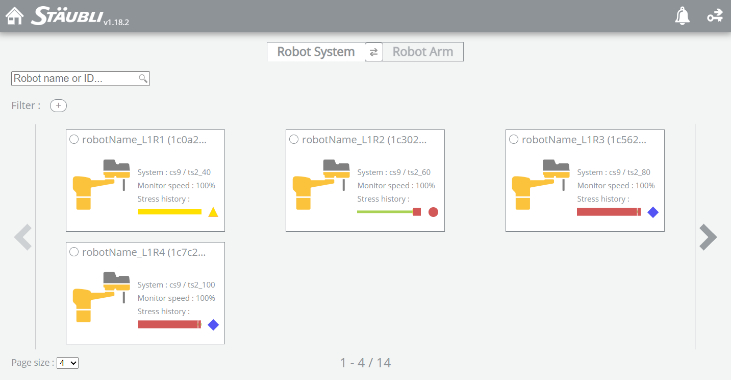
Screen 1 – Displays robots and their status at a high-level view
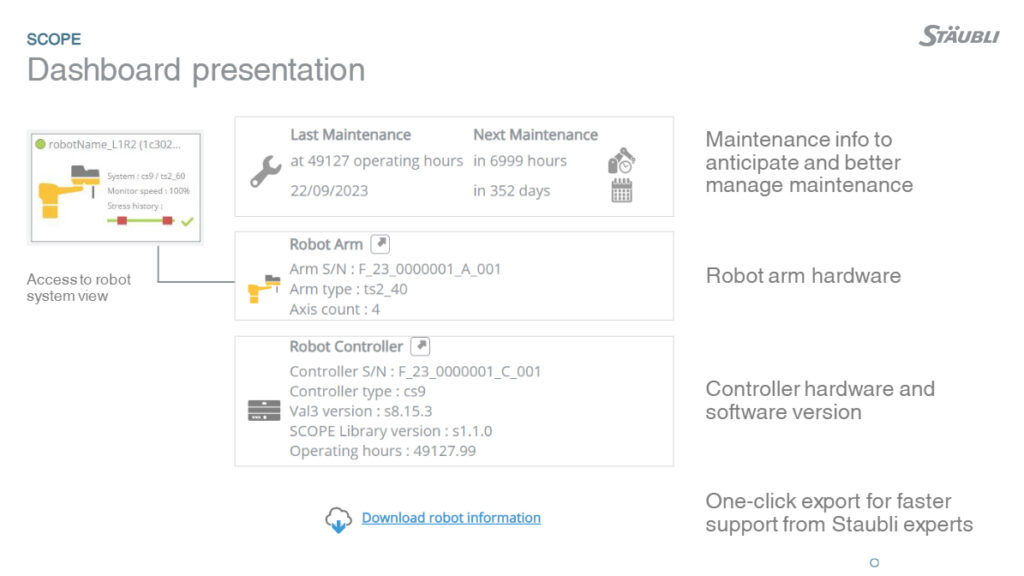
Screen 2 – Individual robot detail, information on arm and controller hardware & software versions. Also operating hours and maintenance information
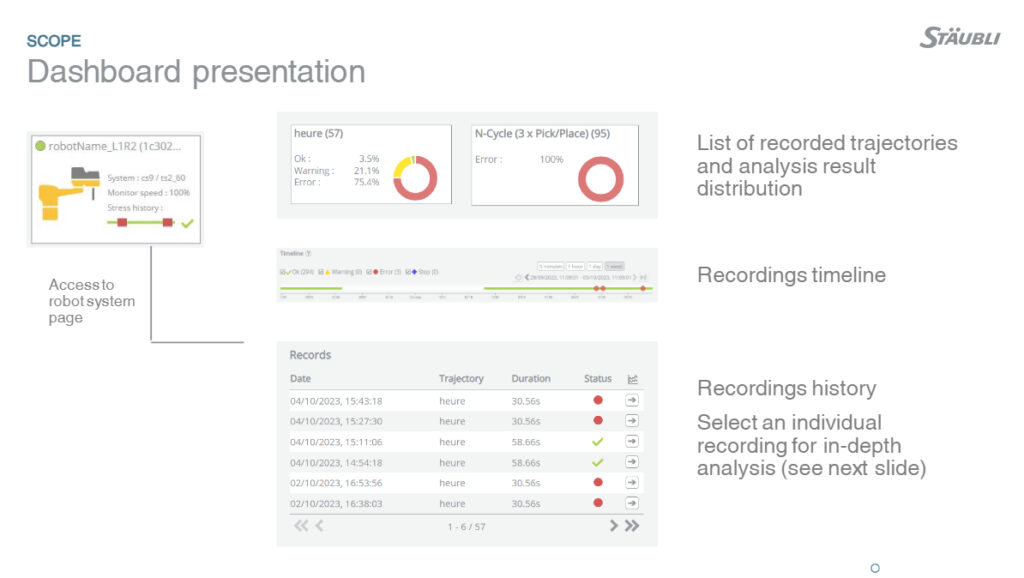
Screen 3 – Displays robot system page, including recorded trajectories, timelines, and record history
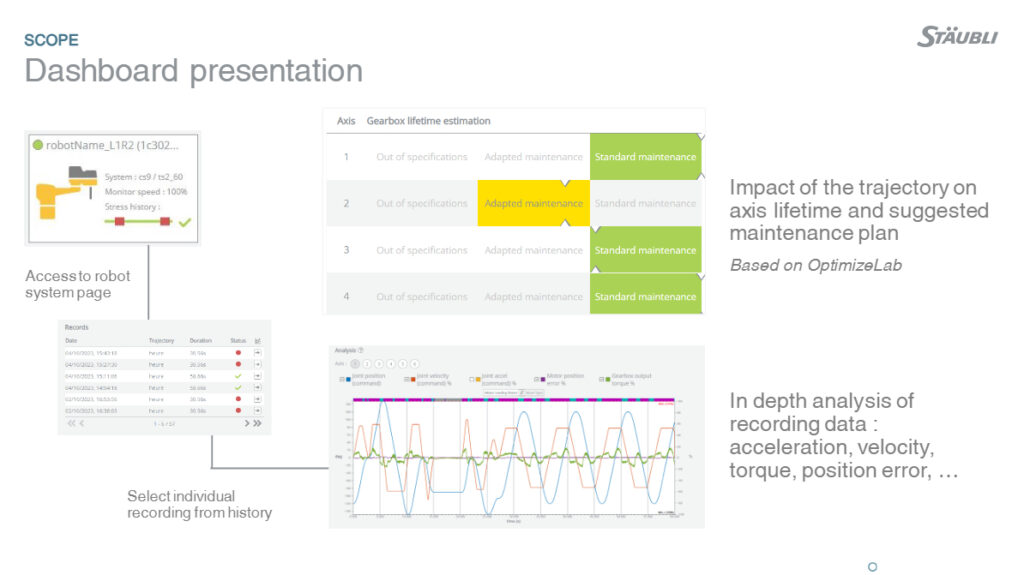
Screen 4 – Impact of trajectories on axis lifetime, plus suggested maintenance plan. Also, an in-depth analysis of acceleration, velocity, torque, and position errors etc.
Staubli’s Simon Jenkins comments: “The implementation of SCOPE makes it possible to detect issues ahead of time and before they even present themselves as a problem. By facilitating smarter and more efficient processes, manufacturers benefit from both reductions in downtime and increased lifecycle from their robot systems whilst making further progress towards the ambition of zero downtime.”