The quest for greater efficiency and digitization is more pronounced in automotive manufacturing than it is in any other industry. Early on, it recognized the trend toward electrification in manufacturing processes, and saw the potential to replace inefficient pneumatics. In the case of body construction, it’s possible to show effective production solutions as, at the moment, automation technology is particularly challenging.
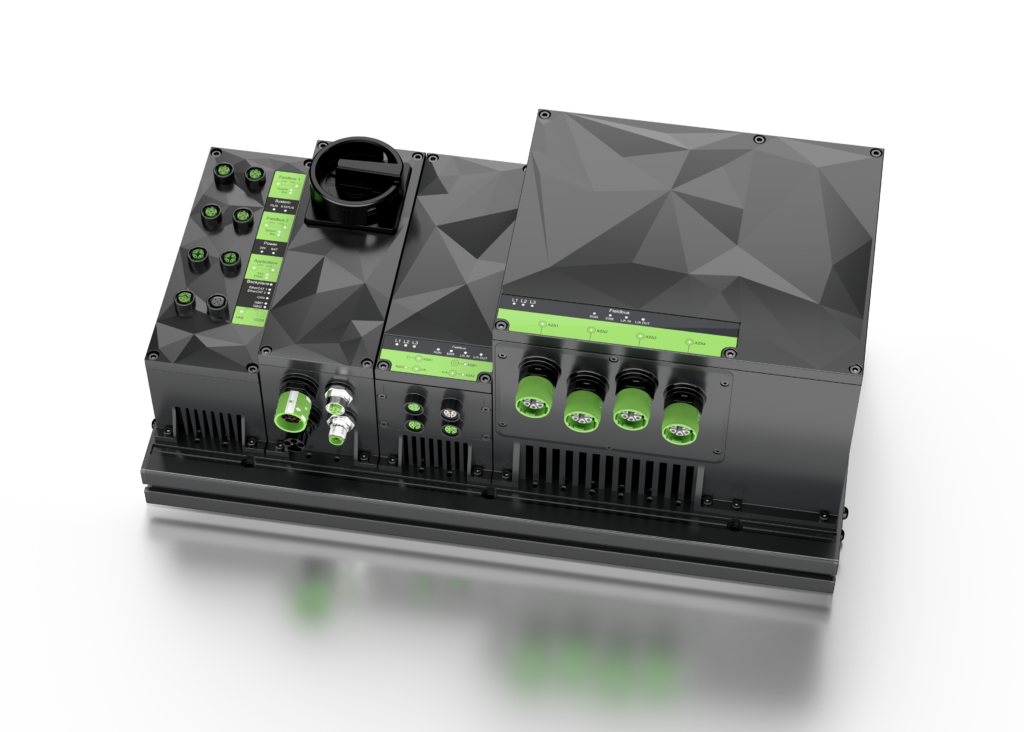
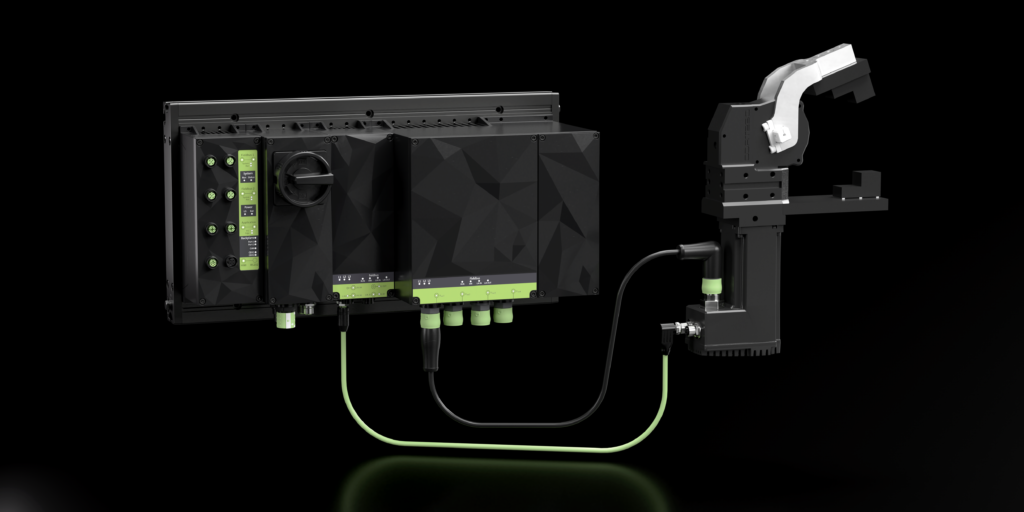
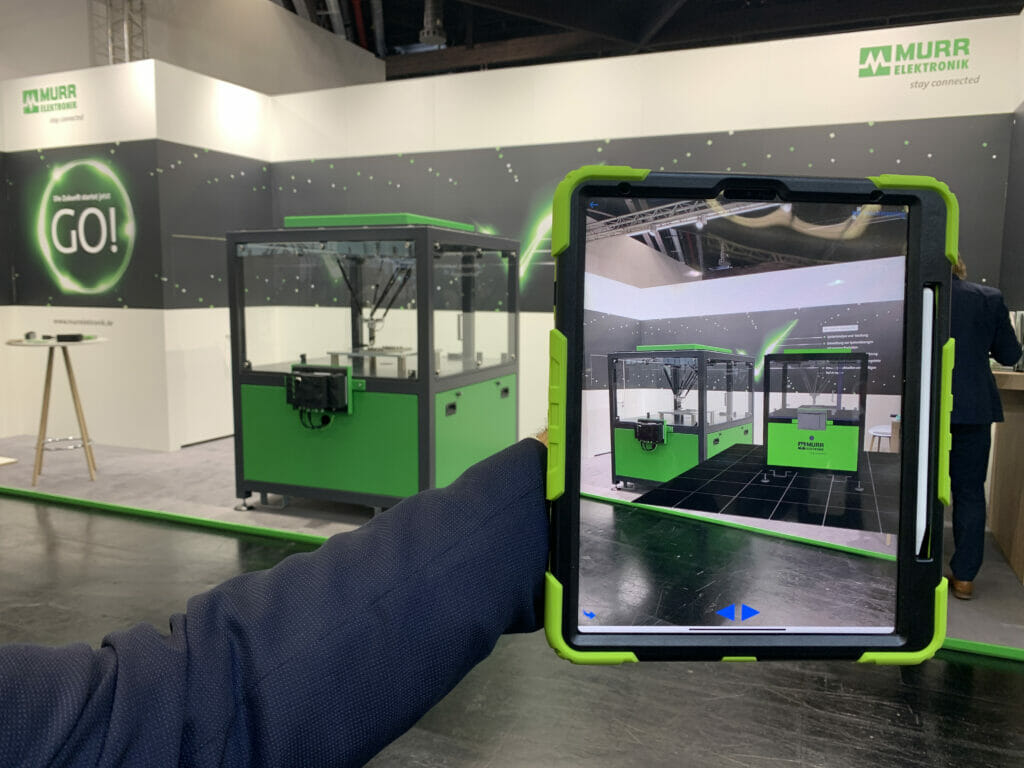
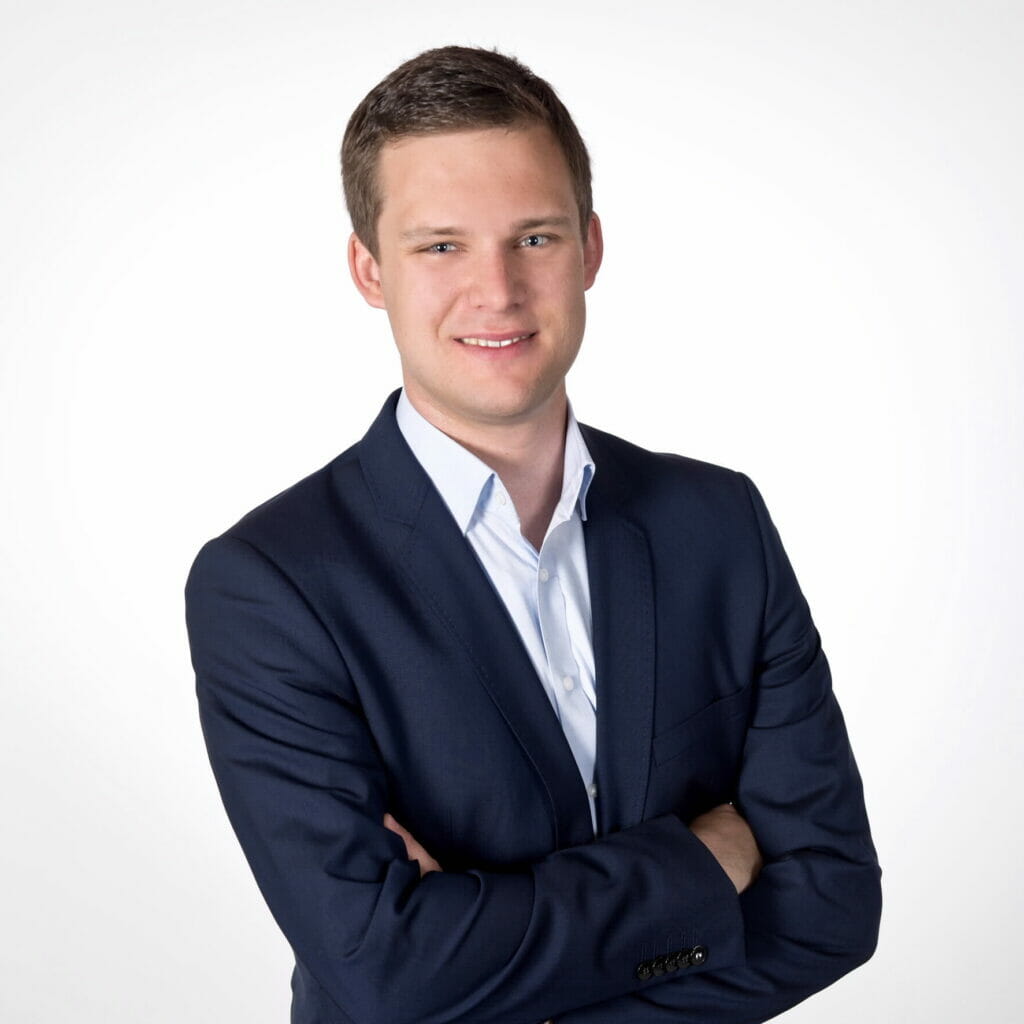
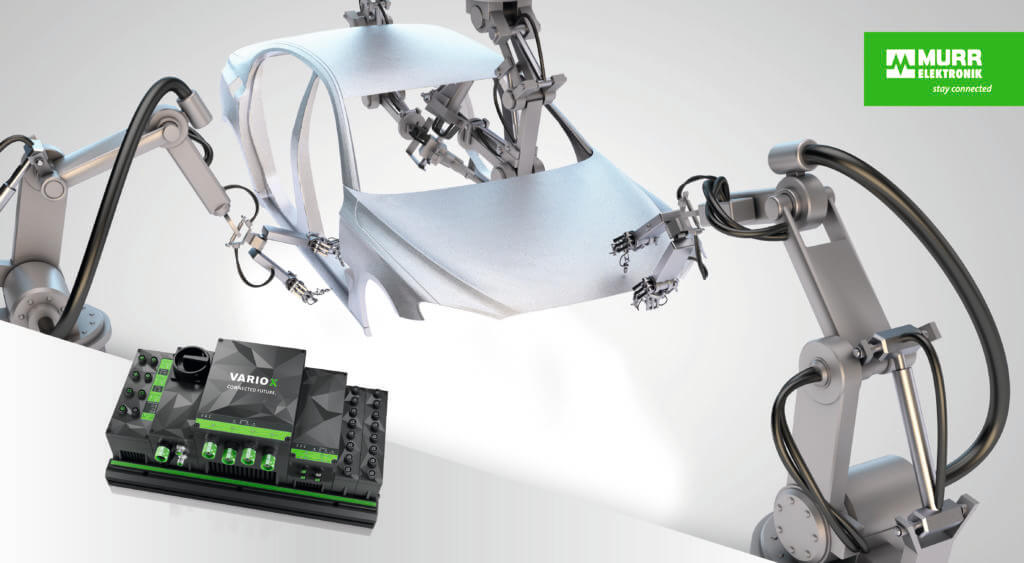
By Christian Kübler
Classic wiring is the biggest cost factor when installing control cabinets. It accounts for more than 50 percent of the installation costs. The combination of modularization and prefabricated connectors has provided a considerable leap in efficiency while minimizing wiring errors.
Decentralized automation concepts create seamless integration of decentralized servo drives because they bring both the power supply and the devices where they are needed. With this approach, the control cabinet has become obsolete which brings a whole range of advantages.
Fit for the future with lean installation concepts
It is high time to face the challenges of tomorrow’s production world and find the right answers to questions about digitalization, Industry 4.0, artificial intelligence, the skilled worker shortage, and the expectations of future generations regarding New Work. Flexibility and time-to-market are also gaining in importance in manufacturing and are shaping plant design along with questions about energy efficiency, CO2 reduction and sustainability. So pretty much everything that has been relied on in manufacturing processes to this point is currently being under review.
For automation in car body manufacturing, this means getting out into the field, decentralizing, modularizing, combining technologies, becoming more energy efficient, and simplifying. The basic idea behind decentralization is as simple as it is obvious: First, the power supply, as well as other standard components like fuses or circuits, are removed from the central control cabinet and packed into smaller, decentralized enclosures. Those are then placed directly on the machine. The same applies to the industrial PCs, which handle communication and control of the entire system or of individual, modular machine parts. Another advantage is simplified installation as, ideally, devices become plug-and-play thanks to pre-assembled connectors. This eliminates the need for complex, time-consuming work at the control cabinet, like stripping, setting wire end sleeves and making the actual connection. This frees production and manufacturing halls from machine attachments and significantly streamlines the cable architecture.
Efficient all along the line
In the halls of the body shop, there is still a lot of hissing and whistling going on. Good old compressed air still drives the pneumatic clamps there. Every hiss and whistle is proof that pneumatics are a less than ideal way to get things done. With an efficiency of only 10 to 20 percent, you can hear the air being wasted via unavoidable leaks and inefficient actuators. And, to make a bad situation worse, compressed air is expensive.
Replacing pneumatic clamps with electric clamps offers advantages for all:
- The automaker can reduce inefficient, poorly controlled, and relatively expensive pneumatics in its plants.
- The production planner can now focus on a single energy source – electricity.
- Employees work in a noticeably quieter and healthier (compressed air releases an oily mist) environment.
Finally, in contrast to pneumatics, process data including the position of the mechanics, or the required torque, can be recorded and analyzed during the motion cycle when using servo motors. They replace the measuring systems and limit switches. Double sheets can be detected in this way. Commissioning is 80 percent faster thanks to simple “teaching” instead of “shimming”. Additionally, multiple clamping points and variant production with different material thicknesses – keyword batch size 1 – are possible without new teaching. Pneumatic clamps, on the other hand, must be readjusted several times a week. This pays off in terms of sustainability and CO2 targets because regenerative electric clamps save energy, which in turn protects the environment.
Fast installation, flexible application: Vario-X
The prerequisite for decentralization in body shop is a systemic approach involving a combination of design and hardware. On the one hand, a comprehensive automation concept includes a systemic view of the challenges and their mutual interactions. On the other hand, modular and scalable hardware that takes over the control cabinet functions and places them at the machine and compliments them in terms of digitization. A solution is offered by Vario-X from Murrelektronik. A modular, flexible automation platform with which all automation functions can be implemented without a control cabinet for the first time on an as needed and decentralized basis.
The application areas in body construction are diverse. From infeed axes to power clamps to lifting units, anything is possible – all driven axes (with a power of up to one kilowatt) can be implemented. Pneumatic actuators can be easily converted to a servo-electric solution with Vario-X. The conventional actuators used in car body construction can be replaced by a servo-electric solution. The common drive powers in body construction (up to approximately 600 watts) are ideal for Murrelektronik’s automation platform which comes with a 48V DC supply. An encoder integrated in the drive eliminates the need to connect limit switches and other sensors. Simply replace the compressed air hose with Murrelektronik’s MQ15 power connector – and you’re done. Another win: compared to the common 560V DC servo drive technology, employees work in a much safer working environment with 48V DC.
Vario-X consists of the platform of the same name and the accompanying automation and installation concept. It brings devices into the machine environment and ensures seamless integration of decentralized servo drives for reliable voltage, signal and data management. At the heart of Vario-X are robust, waterproof and dustproof housings with an IP65 rating, that contain the power supply, controller, switches, safety technology and IO modules. The modular units are snapped side by side into a robust backplane with integrated machine construction profiles.
Digital twins
Digital twins take digitization to a new level. This digital image of the plant or machine contains all the functions and configurations of the system, including the original control software. This is relevant for preliminary considerations such as collision testing of moving parts in body construction. With augmented reality (AR) applications, all motion sequences can be viewed, and analyzed, on a tablet.
During operation, the digital twin provides the data for condition monitoring and predictive maintenance. In this way, production anomalies can be detected and remedied before quality suffers. Long-term analyses enable statements to be made on energy efficiency and simulations of process changes, which provide information on possible savings potentials.
Vario-X shortens commissioning by an average of 40 percent based on a digital twin and its innovative installation concept. In addition, the overall system supports modular and transparent processes, higher value creation, and greater cost-effectiveness and sustainability in body shop. The bottom line is that, with consistent implementation of decentralization, the platform enables entry into digital transformation during ongoing operations – the decisive step in the right direction.
Contact:
Murrelektronik UK
Tel: 0161 728 3133