Kollmorgen has introduced the P80360 stepper motor drive, which offers real-time position correction thanks to closed-loop operation. The new drive provides versatile programming capabilities with extended positional control, while closed-loop feedback ensures improved reliability and efficiency. The Kollmorgen P80360 is also straightforward to control and commission. INMOCO is supplying the new Kollmorgen closed-loop stepper drive to the UK market and can assist OEM engineers with system specification.
The newest drive in Kollmorgen’s P8000 stepper drive platform offers real-time position correction through closed-loop feedback. The new drive includes programmable sequences to achieve more complex motion profiles, similar to servo control. This includes controlled point to point control moves that can be programmed at distinct set speeds and speed ramp profiles.
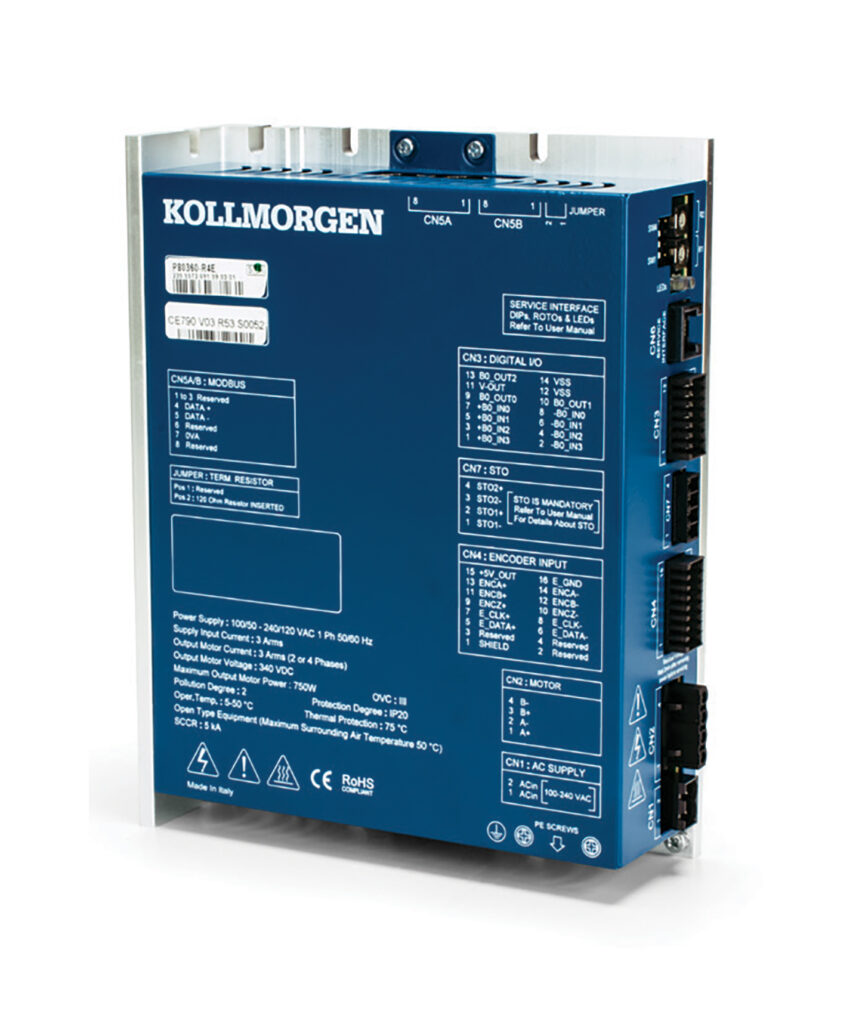
Kollmorgen’s P8000 stepper drive platform offers real-time position correction through closed-loop feedback.
Closed loop control also enhances positional resolution, with 51,200 steps per revolution. As a result of the drive’s enhanced control, the P80360 provides stall detection and can also track load position via encoder feedback, automatically correcting any overshoot or undershoot errors. This functionality is ideal in systems where gearing, couplings or heavy loads could result in missteps with open loop stepper control. Removing the need to over specify the motor to avoid this challenge that is common to open loop specifications, the closed loop drive can safely and reliably operate at a lower current, enabling more efficient and lower temperature operation.
The P80360 stepper drive can be used with all stepper motors with phase current up to 3A peak, and an input voltage of 100-240 VAC single-phase. The drive also runs with Modbus RS485 RTU onboard. Combined with its motion control capability, these features make the drive suitable for applications that require simple point-to-point movements through to linked motion sequences. This includes packaging machines, CNC, XYZ gantries, medical lab equipment, as well pumps that need higher precision control.
Programming the drive is achieved via Kollmorgen’s Space software package, which is free to download. Combined with onboard motion control functionality that removes the need for an external PLC, the Space software package enables straightforward programming of kinematic profiles via an intuitive graphical user interface. Kollmorgen Space also provides commissioning in one software environment, incorporating a motor wizard that matches and autotunes to Kollmorgen motors, only requiring input of the initial profile velocities and acceleration times.
To create a full motion system, INMOCO can supply motors, gearboxes, actuators, and encoders, providing full specification assistance. INMOCO’s engineers integrate regularly with OEM design teams as well as partnering with Kollmorgen’s to give the latest guidance and support.