The main goal of this cooperation is to develop a future ready gearmotors based on ultra-high efficiency EM-A series motors. By combining effort together with Tramec, Mitsubishi Electric is expanding its product range with components for customers seeking high-end drive solutions and improved energy efficiency.
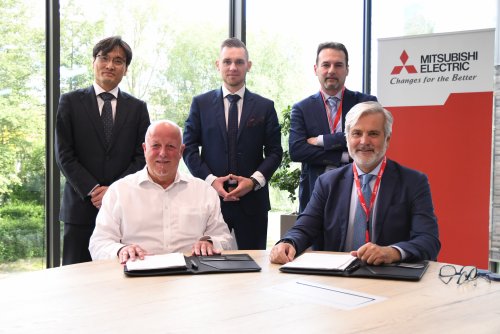
Mitsubishi Electric and Tramec Announce Strategic Partnership, from the left: Masaki Kawazoe, Hartmut Puetz, Wojciech Bracha, Gianfranco Lanzo, Michele Gavino.
New Alliance Powering Manufacturing
Mitsubishi Electric has signed a partnership agreement with Tramec, a European gearbox manufacturer, to supply gearboxes for Mitsubishi Electric’s EM-A synchronous motors. The agreement, formally signed on 22 May 2025, enables Mitsubishi Electric to offer complete gearmotor drive systems that combine ultra efficient IE5+ motors with high efficiency gearboxes. This strengthens the company’s position as a drive systems provider while addressing the evolving needs of the European market. By integrating Tramec’s gearboxes with Mitsubishi Electric’s EM-A synchronous motors, the company can now deliver integrated automation, mechanical and mechatronic components, focusing on energy efficiency and sustainability.
Tramec was selected as a partner due to its reputation in the European market, global operations, and European-based engineering centres, R&D facilities, and manufacturing operations in Italy. This proximity to Mitsubishi Electric’s value chain ensures effective collaboration and product delivery, creating a responsive supply chain that can adapt to market demands and customer requirements.
“This partnership enhances our ability to provide integrated drive solutions,” said Wojciech Bracha, Strategic Product Manager for AC Drives in EMEA region. “By combining our EM-A synchronous motors with Tramec’s high efficiency gearboxes, we’re responding to our customers’ needs for comprehensive and energy-efficient drive systems that integrate seamlessly into their operations.”
The Net-Zero Challenge Response
According to The Manufacturing Momentum Report 2025, 40% of manufacturers now cite net zero as their main sustainability challenge, making energy optimisation increasingly important. With electric motors accounting for nearly 70% of global industrial electricity consumption, manufacturers are prioritising energy efficiency when selecting motors and drive systems. This partnership addresses these industry challenges by providing efficient integrated solutions. “It was estimated by International Energy Agency that globally by implementing high-efficiency motors industry can save up to 10% of global energy consumption. Further 15-25% of energy savings can be achieved by optimization of mechanical systems. This cooperation [with Tramec] is a milestone in our commitment to future energy efficiency optimization across various segments of industrial manufacturing” – said Wojciech Bracha, Strategic Product Manager for AC Drives in EMEA region.
Dual Impact: Transforming Machine Building and Operations
For Original Equipment Manufacturers (OEMs), the EM-A motor solutions with Tramec gearboxes offer practical advantages that improve machine performance. The synchronous motor performance ensures stable speed under fluctuating load conditions, enabling the construction of more reliable machines. The improved energy efficiency adds value to OEMs’ equipment, supporting the development of machines that meet modern sustainability requirements. Additionally, the sensorless positioning capabilities simplify machine architecture, allowing them to optimize costs while maintaining performance standards.
End users of the integrated solutions will benefit from operational improvements and cost savings. The energy efficiency translates to reduced operational expenditure and lower production costs over the equipment’s lifetime. The simplified architecture with sensorless positioning results in improved system reliability and easier maintenance, reducing downtime and service requirements. The stable speed performance under varying loads contributes to consistent production output, addressing a key need in manufacturing environments.