Thankfully, the days of manually handling parcels in warehouse sorting operations are coming to an end. Conveyors have allowed high volumes of items to be moved almost effortlessly around a facility – but they are no panacea. When businesses experience rapid growth, space is limited or sortation becomes more complex, conveyors display clear limitations. In these scenarios, it’s robots from automation experts such as Prime Vision that excel.
The limitations of a static solution
Sortation machines are still the go-to solution for moving incredibly high volumes of parcels, but if an operation doesn’t have this throughput or acres of available space, conveyors make less sense.

In a 2022 study, 23% of businesses surveyed said that they were currently using robots in their facilities.
Conveyors are inherently static and inflexible. This means they can’t really expand with a business unless costly renovations are carried out – a handicap in markets such as e-commerce where rapid growth is the norm. When specifying conveyors, operators need to think years into the future regarding customer demand, as equipment can only be optimised once.
Space is another consideration. Conveyors are large, which when contending with limited real-estate, isn’t ideal. This problem is further exacerbated if there is a wide range of picking or sorting destinations. Moving parcels to all these areas with conveyors would result in a complex jumble of equipment that poses an obstacle to warehouse personnel during an emergency, hindering escape.
The final problem is the disproportionate effect conveyor downtime can have on a sorting operation. An unforeseen breakdown on any part of the system risks bringing the entire process to a grinding halt, resulting in late deliveries, lost revenue and dissatisfied customers.
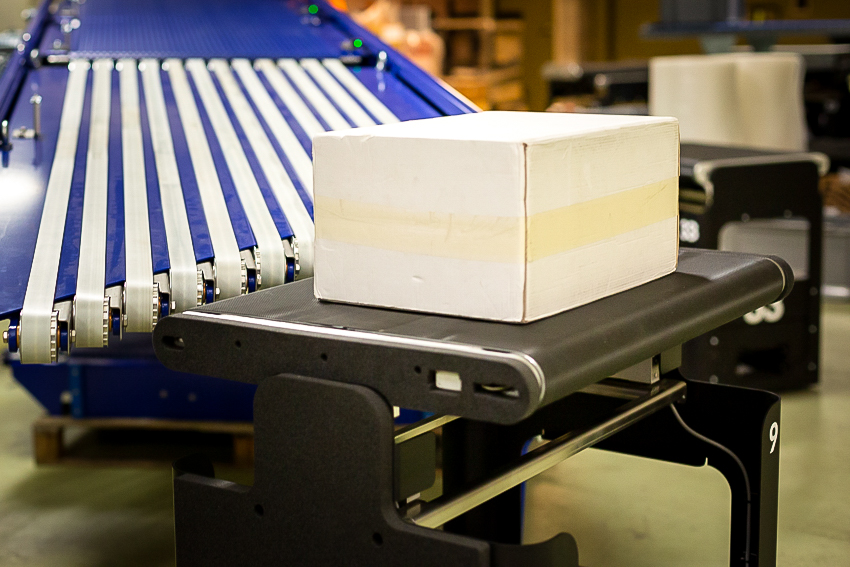
With an 80 x 60 cm loading surface for parcels, Prime Vision robots offer a 35 kg carrying capacity.
A future alternative available today
Flexible and anything but static, robots are proving to be a new, versatile alternative to conveyors for a wide range of logistics operations.
Take Prime Vision robots for an example. Standing 1 m high with an 80 x 60 cm loading surface for parcels, Prime Vision robots offer a 35 kg carrying capacity and the ability to detect items from 100 g. Consequently, they can handle most items encountered in the postal or e-commerce markets.
Guidance is achieved with onboard light detection and ranging (LIDAR) systems, which allow the robots to avoid obstacles and personnel. By mapping out the space that the robots will operate in beforehand, all units will seamlessly navigate within it.
By scanning the barcode on a parcel, the robot will identify the intended destination and calculate the best route to it. An overarching fleet management system plots the position of each unit, then deviates any that might crossover with another, reducing delays. Therefore, any robot can efficiently travel to any picking or sorting destination independently, ensuring exceptional flexibility.
Applying the benefits of robots
With this functionality, robots offer multiple benefits over static conveyors. Operational expansion can be achieved by simply introducing new units to the fleet. Therefore, periods of rapid growth or peak demand are more easily accommodated than with conveyors. Furthermore, if new picking or sorting destinations need to be added, robots can be quickly programmed to drive to them. Robots can handle growth and increased complexity simultaneously.
While they still need room to manoeuvre, robots require nowhere near as much space as conveyors. This means that they are highly suited for sorting operations in smaller facilities. Additionally, unlike conveyors, robots can be easily relocated. With these inherent qualities, they are ideal for localised or temporary facilities set up close to the point of delivery, allowing businesses to optimise last mile logistics.
In terms of safety, robots are preferable too. Single robots or the entire fleet can be deactivated at the touch of a button, and if an emergency should occur, personnel don’t have large conveyors blocking potential escape routes.
Robots are also more robust than conveyors. A single faulty robot can easily be replaced, or other units rerouted to cover for the shortfall, without halting the entire sorting operation. Maintenance can be carried out and the robot returned to service without any service interruptions, saving time and cost. Ultimately, choosing robots over conveyors makes an operation more resilient.
For sortation where high volume and complexity are both factors – robots can easily work together with conveyors, combining the benefits of each to overcome traditional pain points in the sorting process. More than overcoming its challenges, robots integrate with fixed infrastructure too.
Warehouses choose adoption
Warehouse operators are now recognising the benefits of robots. In a 2022 study, 23% of businesses surveyed said that they were currently using robots in their facilities, while a further 21% planned to within the next three years.

Clearly, robots will continue to play an increasing role in future sorting operations.
Prime Vision not only provides customised robots for warehouse logistics, but the system design and training to smoothen adoption for e-commerce companies and postal services. Working on a case-by-case basis, the business creates environments where robots and employees can confidently and safely collaborate. Consequently, robots can become as much of an accepted part of the warehouse ecosystem as conveyors before them.
More from Prime Vision – https://primevision.com/robots-vs-conveyors