A collaboration between SICK Sensor Intelligence and Universal Robots has created the End-of-Arm-Safeguard (EOAS), enabling more effective human-robot collaboration than ever before. A world-first, the patented technology ensures robots and humans can work in closer proximity with improved safety as the technology is mounted directly onto a robotic arm.
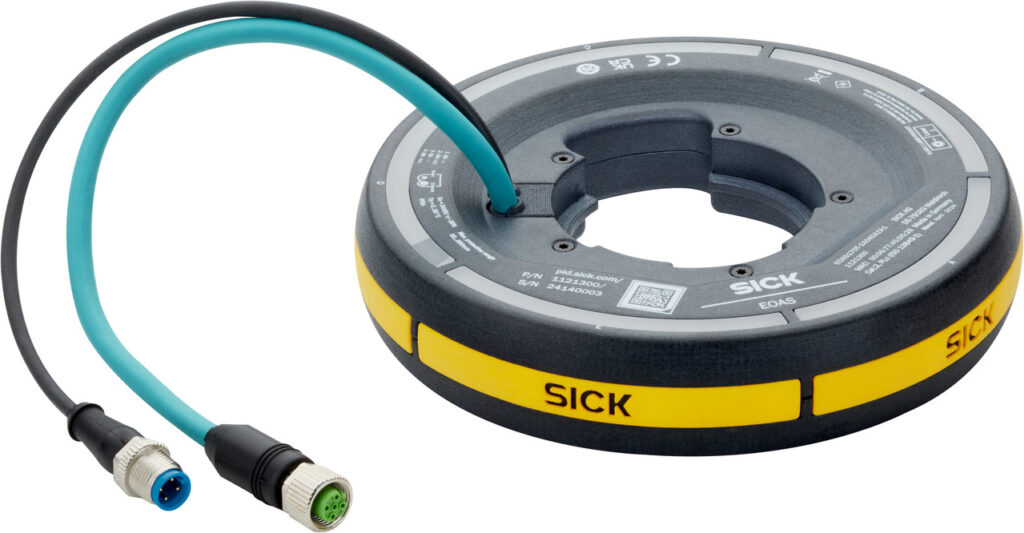
Distributors of SICK and Universal Robots technology are excited by the prospect for safe, collision-free, reliable collaboration between humans and robots across a wide range of industrial settings. Bringing together SICK’s sensor expertise with the world’s largest cobot vendor for seamless teamwork, distributors predict it will generate new sales opportunities and applications.
Gavin Ford, Sales Manager at Applied Automation UK, has been working as a Universal Robots distributor for more than five years. He immediately sees the benefits of the EOAS “from a technical aspect. From a price aspect. From an operator’s aspect”.
Safer operation and peace of mind for operators
With the EOAS, when the protective field is breached, a Safe Stop is triggered and the cobot immediately ceases movement, recommencing its task once it is restored. Lights on the EOAS indicate clearly when it has stopped and when it is moving, providing extra peace of mind for operators to work more closely and collaboratively with cobots. Time-of-flight technology provides a response time of ≤110 ms, speeding up productivity while maintaining safe operation.
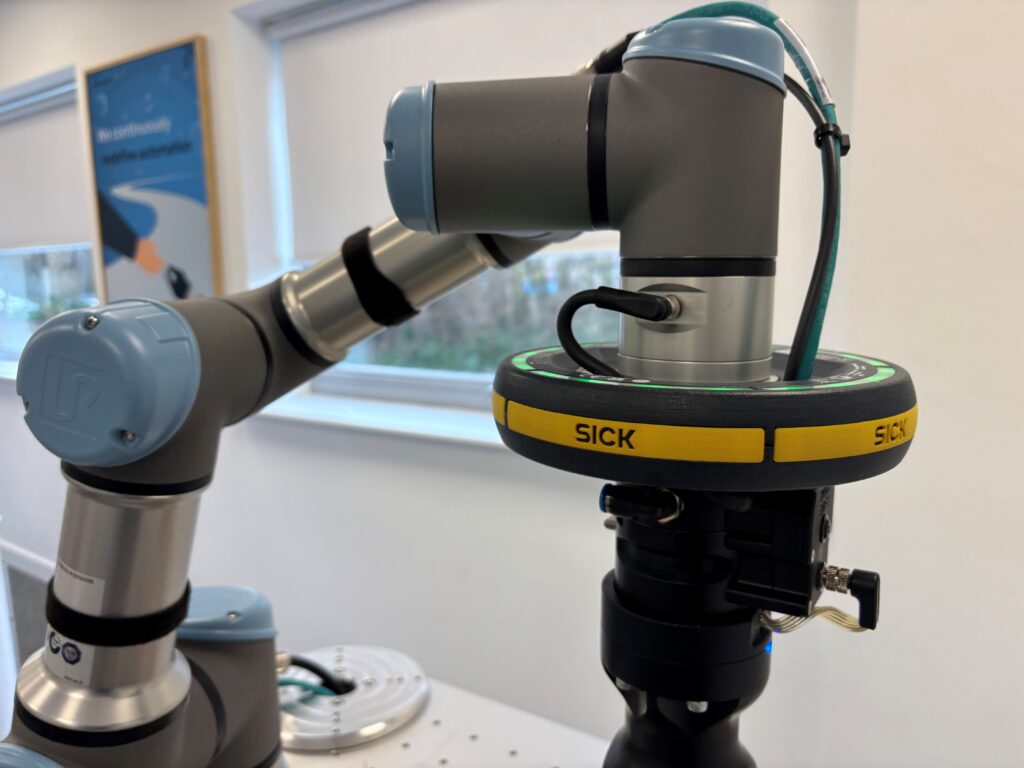
Mark Stephenson, Divisional Manager at WMH Robotics, notes: “The EOAS makes the operation status of the cobot clear; it’s either red or green. It has been developed as a true partnership between SICK and Universal Robots, with all the benefits of both companies. We will see cobots working collaboratively as they were intended to; making people more confident about getting closer to the machine and being more interactive with it for safe productivity.”
Fewer stops, greater efficiency
Creating a protective field around the robot tool at the end of the robot arm, the EOAS moves with the arm and operates in a much smaller, more defined area than previous products to protect a fixed hazard range of up to 400 mm. As factories become busier and more fluid, with greater use of AMRs, AGVs and mobile workstations, mounting the sensor directly onto the arm of the cobot means unnecessary stops are kept to a minimum. Mark Stephenson predicts, “The EOAS will result in a lower number of false triggers and false Safe Stops. It won’t stop until you are at the point where it is potentially hazardous.”
Potentially reducing the need for additional safety measures
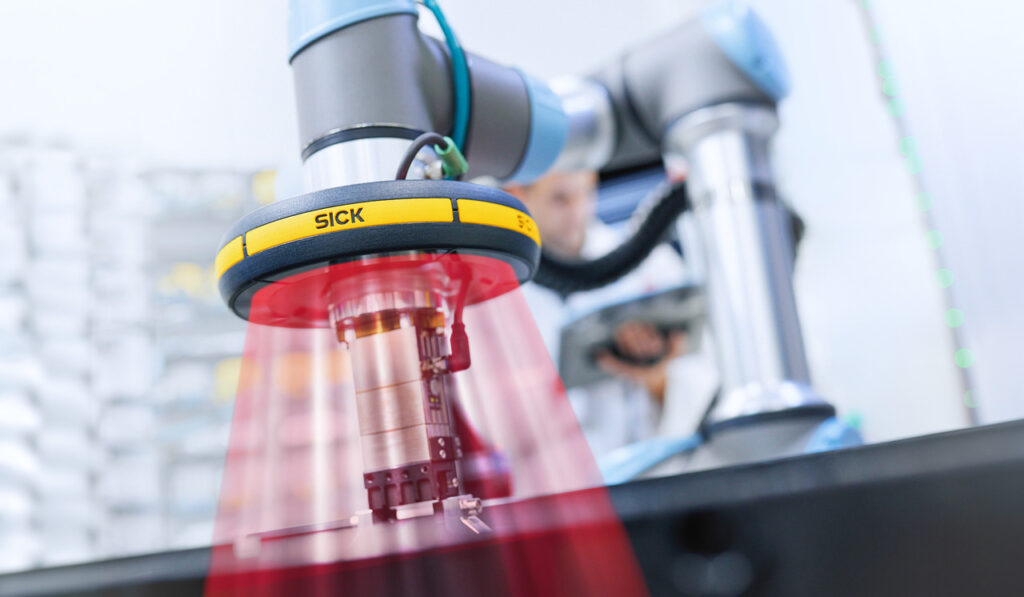
According to distributors, one of the key benefits of the EOAS is the potential to remove additional safety measures for applications, such as physical guards. The EOAS provides a Safeguard Stop through an invisible, infrared, protective shell of 40 laser beams that covers the tool and workpiece to facilitate space-free operation. As industrial real estate costs climb, the most expensive thing in many factories is floor space. Allowing humans to work more closely and efficiently alongside cobots by protecting the end effector, potentially without the need for mechanical or light guards, significantly reduces the safe zone of the cobot and therefore the overall footprint, length and cost of projects. Ross Lacy, Sales Director at RARUK Automation, explains, “It’s much easier to put into small environments. In the UK you don’t exactly have much space at the end of the line, so anything that reduces the footprint and the size of the cell is a huge benefit.”
Compatible with URCap software and easy to install
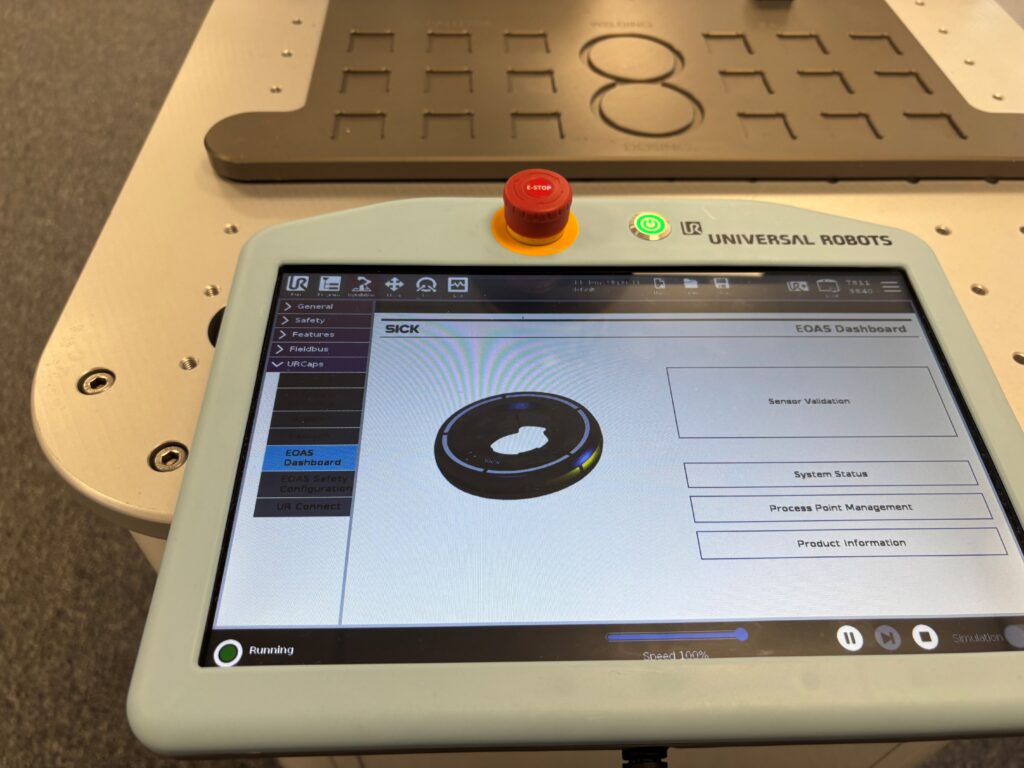
The EOAS can be installed in just 15 minutes and the sensor is automatically recognised by Universal Robots technology. Configured using EOAS URCap software and provided with automatic updates, the EOAS makes it easier for customers to protect end effectors and create safer, more collaborative human-robot applications. As Ross Lacy states, “There’s no additional software for the end user or the integrator as it can be programmed directly from the Universal Robots pendant. Anything that can make the risk assessment easier for the customer to carry out and to do their own internal CE marking is a huge bonus for us. It’s great for small businesses as well as large corporates because it’s cost effective and easy to install.”
A wide range of scenarios anticipated for the EOAS
Distributors see a wide range of potential markets and applications for the EOAS, in sectors ranging from pharmaceuticals and electronics, to food & beverage and automotive. Ideal for machine tending and pick and place applications such as presenting components to operators for assembly or where there’s multiple picks of parts, the EOAS can also be installed on a collaborative robot arm that is mounted on a mobile robot, reducing the number of false stops for the robotic arm and creating greater flexibility within industrial settings. Gavin Ford predicts, “I think the EOAS will open up a lot of opportunities for us in applications such as machine tending and pick and place by making them more collaborative. It’s a good product and a good solution and I can’t wait to start looking at applications for it.”
Combining Universal Robots and SICK Sensor Intelligence expertise and available now
Matthew van den Braak, Product Manager – Robotic & Mobile Platforms at SICK UK, says: “The EOAS is making collaborative robots more effective and affordable for end users. With the EOAS, you can work really close to it and interact with it. It is completely new technology that has been developed in partnership and is fully compatible with Universal Robots products.
“We are delighted with the buzz this brand-new patented technology has created among distributors. I look forward to seeing the wide range of different applications it is used for and the challenges it meets. The EOAS is available and in stock now, with a lead time of just three days.”