Mark Moore of Moore International, specialists of thread drives, provides some guidance.
Ballscrew basics
Rotary motion can be converted to linear motion through use of a ballscrew, whilst at the same time converting torque to thrust and vice versa.
Ballscrews can move heavy loads with both high speed and accuracy. Apart from the train of hardened ball bearings that enable rotational motion, the ballscrew consists of two main components, the threaded shaft and the nut, either of which can act as the traversing component.
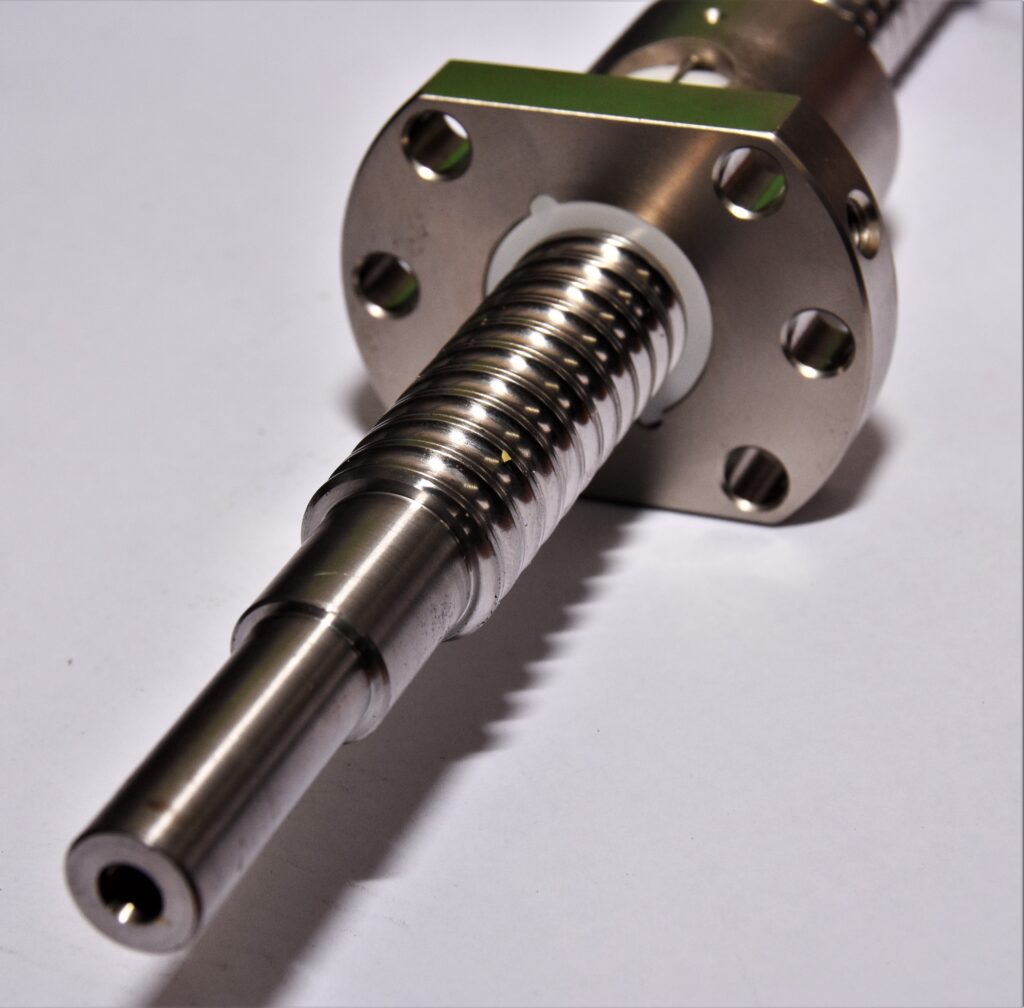
Manufacturing process
Ground and rolled ballscrews are both available in a wide variety of lengths, diameters and load capacities. However, although they may seem to operate in application in almost identical fashion, they are differentiated by their respective manufacturing processes.
A rolled ballscrew is formed by passing a round bar through rotating dies in a single operation. This procedure is a cold work deformation process where the dies compress the bar and form the groove shapes, pushing the material out of the way. No material is removed in this operation, making this rolling process highly efficient and economic. However, rolled screws will also need to be polished to remove any oxidation layers that may have formed during the rolling process.
After the threads have been rolled, the bar is heat treated. This does have the disadvantage of possibly distorting the rolled threads due to unpredictable material expansion rates in the geometry of the thread. In addition, as the end journals are machined and ground after rolling, maintaining concentricity and run-out is more difficult to achieve.
Ground screw threads are formed by a cutting process and the use of a very hard abrasive cutting tool. This tool moves along the length of the of the horizontally positioned bar on lathe centres, carving out a few threads of the screw at a time. For ground screw threads the material blanks typically undergo heat treatment before the threads are ground onto the blanks and is performed using the same reference centres. This helps to keep all the centres aligned, minimises radial run-out and keeps the screw threads and end journals concentric, as well as ensuring that the heat-treating stresses are kept to a minimum. This process is employed for both internal and external thread cutting of the lead screw and ball nut. This progressive abrasive machining process requires the material blanks to be cut to final length before grinding.
Design features
As with any steel-on-steel design, life expectancy will be defined by the lubrication, the mounting and installation procedure and the ability to reduce contamination. The use of wipers on the nut and the fitting of a bellows to cover the screws will help to purge the thread drive of dirt and debris.
Critically, in terms of the application, the accuracy requirements of the system will determine the choice of either rolled or ground ballscrews. When a particular screw is more accurate, the nut will move more smoothly along the shaft of the screw. Straightness, bearing journal concentricity, preload torque consistency nut squareness are all essential to achieve the necessary level of accuracy.
Ground screws are necessary when the ballscrew accuracy below P5 is required, as the rolling process cannot produce these accuracy classes. The lower the number, the better the accuracy, with precision classes ranging from P0 to P5.
Strengths and limitations
As the rolling process is a single pass process, any fabrication errors in the rolled screw threads will be almost impossible to rectify. The surface finish on a rolled thread is always likely to be rougher than that of a ground thread and can be inherently challenging to the performance and mechanical efficiency of the ballscrew. This is because of the rolling friction incurred and overtime may mean a reduction in the wear resistance of the ballscrew.
Another limitation of the rolled screw is the possibility of dimensional distortion caused by wear in the tool die. Not only could this lead to a limitation on the positional accuracy that the system can achieve, but also may develop excessive backlash due to discrepancies between the bearing diameter and the screw shaft thread.
Summary
When deciding which of the two ballscrew options to choose, accuracy and the precise nature of application performance tends to dictate the choice will lean towards a ground ballscrew. However, there may also be budgetary constraints.
There is no doubt that rolled ballscrews will provide substantial savings, because of the efficient production method in comparison to the ground type.
Mark comments “in summary, for a high degree of precision and repeatability a ground screw is your choice. For price, the choice will be a rolled version. However, be aware that the best grade of a rolled ballscrew can be as efficient as the lowest grade of a ground ballscrew and that then becomes a cost effective option”. Custom made rolled nuts can be produced to suit a specific application. By converting a standard nut into a special bespoke shape, customers do not then have to make their own housing nut surround, and the minimum order quantities can be as low as 250 pieces.