The high torque density and enhanced cooling capability of slotted miniature brushless DC (BLDC) motors are instrumental in numerous applications ranging from robotics to consumer electronics. However, to optimise the efficiency, performance and reliability of the application, their specification requires careful consideration. Engineering integration advice in the selection of off-the-shelf slotted BLDC motors is advantageous, and considerations on bespoke design will benefit the application’s performance in the long-term.
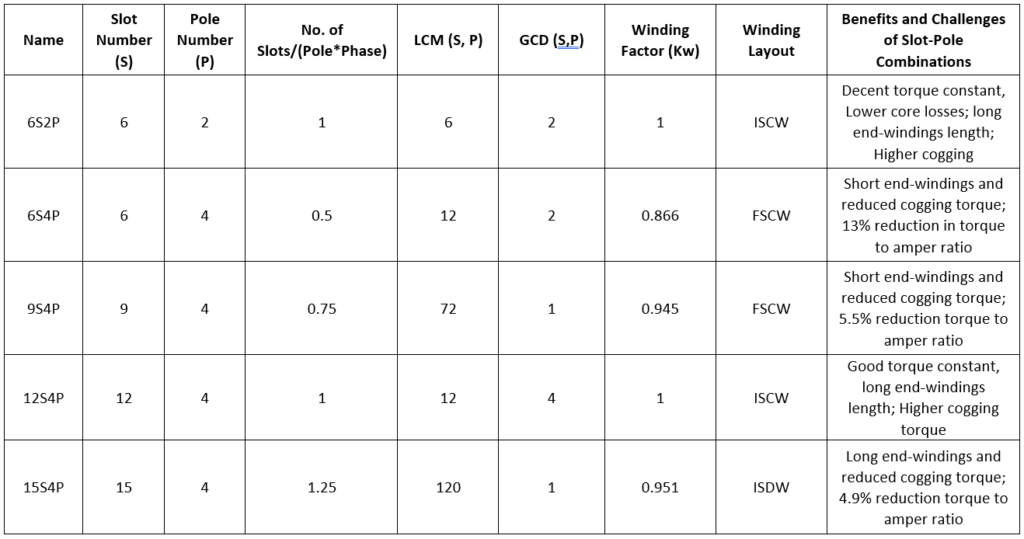
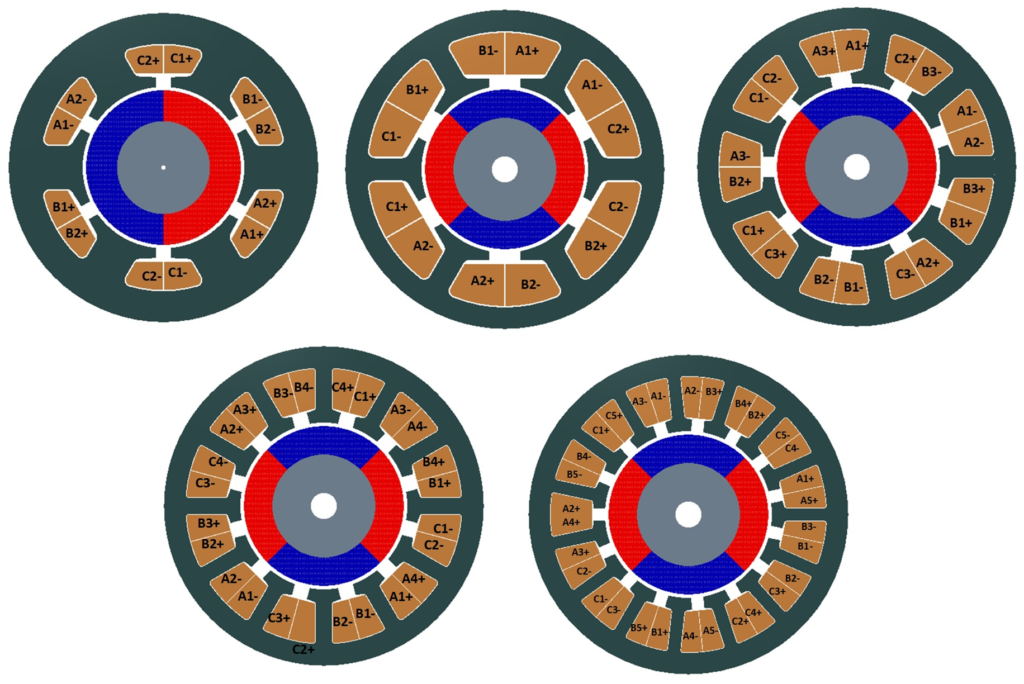
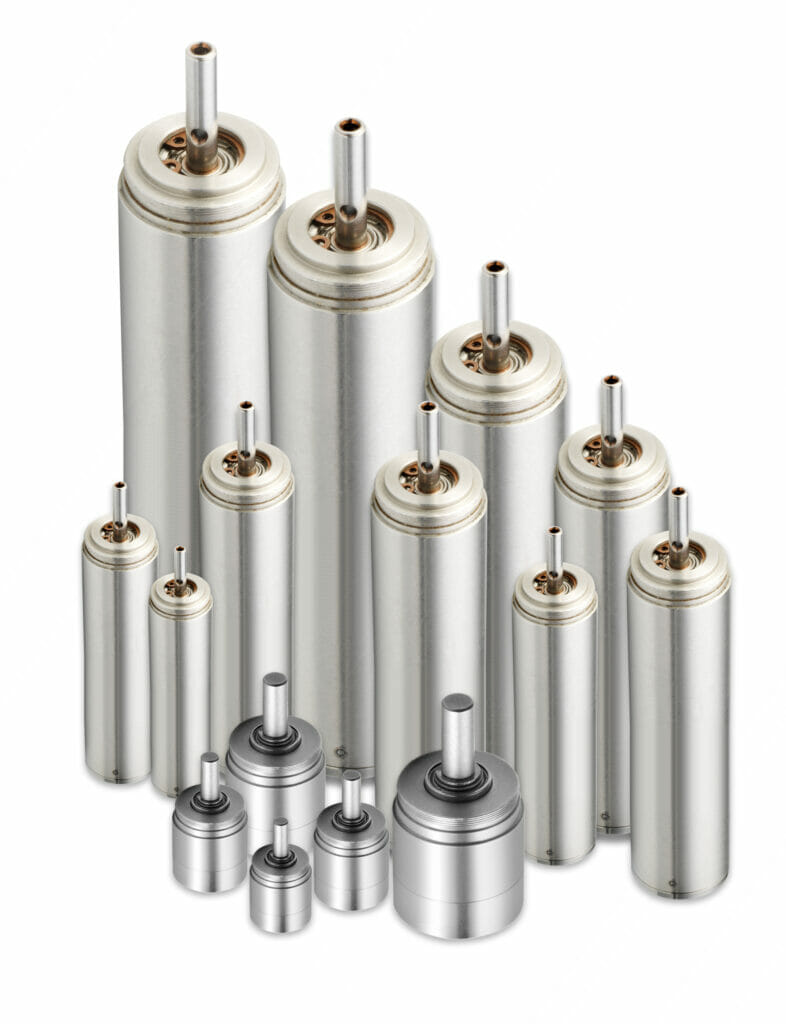
By Dr Madhavan Ramanujam, Senior Principal Design Engineer, R&D at Portescap.
With the absence of brushes for the process of commutation, miniature brushless DC motors have advantages over their brushed counterparts, including improved efficiency, longer lifespan, and opportunities for improved control. Within BLDC motors, there is a design choice for either slotted or slotless configurations.
The stator, which is the outer stationary part surrounding the rotor, contains the windings that channel the flow of electric current. This generates a magnetic field that interacts with the rotor’s magnets, causing it to rotate and create motion. In a slotless BLDC motor, the windings are typically secured in the stator by a resin, or they are held in place by a tape or mechanical retention device. Alternatively, in a slotted design, windings are retained within slots or grooves.
Slotless motors are generally more compact, and these designs are also beneficial for applications that need the smoothest operation and high speed. However, slotted BLDC motors enable an increase in the amount of magnetic flux density in the airgap, which results in higher torque generation; this helps improve the motor’s dynamics, making this design more reliable. The slots also help to dissipate heat, enabling improved cooling.
Sizing slotted BLDC motors
However, slotted BLDC motors present unique challenges during the design phase, meaning that careful specification is required. This includes accurate core loss calculation, as well as the accountability of material saturation and magnet demagnetisation at higher operating temperatures, which can impact performance, efficiency, and thermal management. Sizing the motor to meet the torque requirement is a critical step. This calculation depends mainly on the electric and magnetic loadings, alongside rotor and stator dimensions and the materials selection.
As a broad principle, if the application’s working points involve high speed and low torque, magnetic loading must be optimised to lower core losses with a smaller number of pole pairs. Core losses, also known as iron losses, refer to the energy dissipated in the motor’s magnetic core as a result of the phenomena of hysteresis and eddy currents. At the other end of the scale, if the working points include low speed and high torque, the electrical loading must be optimised to deal with copper losses (also known as I²R losses). Copper losses represent the resistance of the windings to the flow of electric current, and present as lost power in generated heat. Lowering core and copper losses will optimise motor efficiency for the given torque-speed working points.
Torque is proportional to the size of the motor for the chosen loadings and slot-pole combinations. As a result, the selection of loadings and slot-pole combinations is dependent on the application’s torque-speed requirements.
An overview of slot-pole combinations
The arrangement and relationship between the stator slots and the permanent magnet poles on the rotor is known as the slot-pole combination, which describes the motor’s magnetic field interactions.
There are different slot/pole combinations possible with miniature slotted motors. A high winding factor should be considered to increase the torque constant of the motor. A high LCW, or Least Common Multiple, between the number of slots and poles reduces the cogging torque magnitude, while a high GCD, or Great Common Divisor helps to reduce the unbalanced magnetic radial forces and increase the radial symmetry.
A traditional integral-slot distributed-winding (ISDW) two-pole slotted design is possible but the torque constant is lower than a four-pole design, so this option is not recommended for high-torque, low-speed applications.
Various combinations are available dependent on the desired torque and speed, as well as the motor’s ability to deal with characteristics such as cogging torque, which creates torque ripples and impacts the smoothness of motion delivery.
In addition to the slot-pole combination, another configuration, known as fractional slot concentrated windings (FSCW), includes multipole ring magnet configurations. This involves short magnetic circuits and is a design suitable for low speed, high torque applications.
Specifying miniature slotted BLDC motors
The motor’s generated torque is proportional to its volume, the magnetic and electrical loading, and its slot-pole combination. Specifying these characteristics is dependent not only on the application’s torque-speed requirements, but also wider attributes that can impact motion performance, as well as reliability and longevity.
When specifying a slotted BLDC motor, off-the-shelf stator slot shape patterns and standard magnet configurations developed over many years of production can provide high reliability and sufficient performance if the motor size is standard. However, this traditional design typically has suboptimal utilisation of the magnetic circuit, which also means lower efficiency at certain torque–speed working points.
Considering the array of factors that impact specification, seeking engineering integration support from a motion specialist such as Portescap is crucial. This is especially the case for higher volume OEMs. Bespoke motor design is extremely beneficial, as this approach can optimise performance and efficiency for the specific working points; based on customisable existing designs, time to market is often faster than using an off-the-shelf design when all stages of integration are considered. Slotted BLDC motors can also be specified for their cost-effectiveness, and considering the increased value that a bespoke design can provide, this process has a potential of lowering total costs.
To find out more about brushless DC motor specification and designs tailored to your application, contact https://www.portescap.com/